我们知道在公司运作流程中对于处理问题的发生有结构化的方法,提供了一套符合逻辑的解决问题的方法,在设计与生产产品的流程与实际的产品质量提升构成了连接作用。
汽车行业中有以下的一些方法
8D:Ford Motor Company
7D:DaimlerChrysler
5P:General Motors
8D的内容:
D1:成立解决问题的小组,确认小组成员
D2:明确问题的描述与说明
D3:实施并验证临时措施
D4:确定并验证问题产生的根本原因
D5:选择和验证永久解决问题的纠正措施
D6:实施永久解决问题的纠正措施
D7:预防问题再此发生的措施
D8:小组任务结束
7D报告中只少了第七条:预防问题再此发生的措施
通用的5P报告
P1:明确问题的描述与说明
P2:实施并验证临时措施
P3:确定并验证问题产生的根本原因
P4:选择和验证永久解决问题的纠正措施
P5:实施永久解决问题的纠正措施
总结起来,以下的一些东西基本都是需要我们需要注意的,在设计以后,产品如果发生了任何问题,就需要我们采用结构化的方法去解决问题。
1.明确问题的描述与说明目的:用量化的术语详细说明与该问题有关的内/外部顾客抱怨,如什么、地点、时间、程度、频率等。
这是以“黑盒子”的角度去描述问题的状况,最关键的要点在于产品失效的特征,何时何地发生这种问题。
关键要点:收集和组织所有有关数据以说明问题,审核现有数据,识别问题、确定范围,细分问题,将复杂问题细分为单个问题,问题定义,找到和顾客所确认问题一致的说明,而原因又未知风险等级
重点:描述问题的严重度,多少车发生问题
2.实施并验证临时措施目的:保证在永久纠正措施实施前,将问题与客户隔离开来,引起进一步的困境。
关键要点:给出时间计划,给出必要的修正措施,找出和选择最佳“临时抑制措施”,验证(DOE、PPM分析、控制图等)
3.确定并验证根本原因目的:用统计工具列出可以用来解释问题起因的所有潜在原因,将问题说明中提到的造成偏差的一系列事件或环境或原因相互隔离测试并确定产生问题的根本原因。
鱼骨图
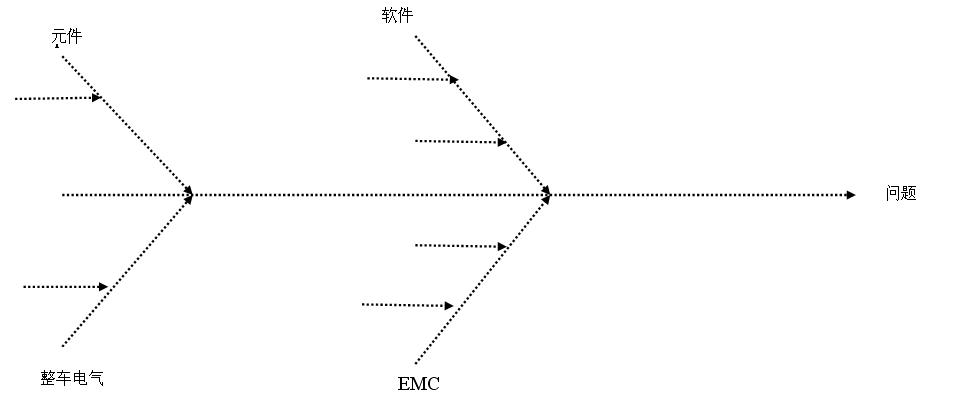
是和不是图
关键要点:
评估可能原因列表中的每一个原因
原因可否使问题排除
记录所有设计与生产流程中的变化
选择并验证永久纠正措施目的:在生产前测试方案,并对方案进行评审以确定所选的校正措施能够解决客户问题,同时对其它过程不会有不良影响。
关键要点:长期修正:a.防呆与防错 b.控制计划
决策,选择最佳措施
重新评估临时措施,如必要重新选择
管理层承诺执行永久纠正措施
实施永久纠正措施目的: 制定一个实施永久措施的计划,确定过程控制方法并纳入文件,确保使问题发生根本原因的消除。在生产中应用该措施时应监督其长期效果。
方法:防错、统计控制
关键要点: 执行永久纠正措施,废除临时措施
利用故障的可测量性确认故障已经排除
控制计划、工艺文件修改
预防问题再次发生目的: 修改现有的管理系统、操作系统、工作惯例、设计与规程以防止这一问题与所有类似问题重复发生。
关键要点: 选择预防措施,验证有效性,组织、人员、设备、环境、材料、文件重新确定
Lesson Learn数据库
确保问题不会再次发生:如果有设计与生产的流程,确保工作人员都能遵守
培训计划
当产品在各个不同的阶段发生问题以后,甚至SOP以后,出现问题,一般需要我们去解决问题,以上的报告是一种格式化的工具,用来正式的提交给客户,对于我们设计工程师来说,以一种结构化的解决问题的思路,也是我们硬件设计工程师在设计的方案出现问题的时候,解决问题的非常好用的工具,对于我们来说,需要以简单的方法把一个个元素整合出来,总体来说,汽车产业和汽车零部件行业就是经历着一次次的8D和5P成长起来的,我们不可能去回避这个事实,当然如果你很幸运的没有遇到这个问题,或者以非正规手段去解决问题,偶觉事关人命安全的事情,还是得不出岔子。
丰田的质量问题就已经说明了问题,未来面对它和它的零部件供应商,这是一个巨大的问题,将来怎么收场,偶觉得还是值得去关注的。
文章评论(0条评论)
登录后参与讨论