要回答这个问题,我们先了解一下盘中孔到底是什么?
其实简单来讲,就是在焊盘中间打个过孔,那这个在焊盘中打孔的好处和害处到底是什么?我们在实际项目中该怎么权衡?
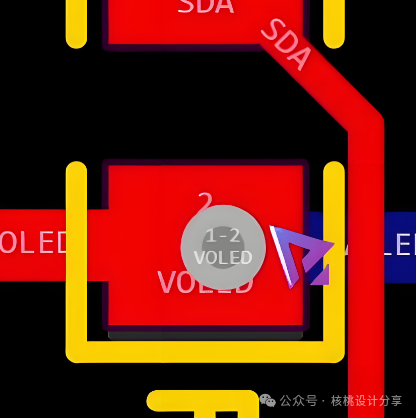
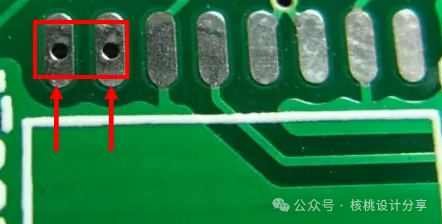
盘中孔的主要害处:
(1)漏锡导致焊接缺陷
未处理的通孔在SMT焊接时,焊膏可能流入孔内造成正面焊盘锡量不足,引发虚焊、脱焊或元器件“立碑”现象。此风险在小封装元件(如0402电阻)及BGA焊盘中尤为突出。
(2)冷撕裂(缩锡开裂)风险
当BGA角部焊盘的盘中孔未连接内层大铜皮时,在流焊快速冷却过程中可能因焊点单向凝固及BGA翘曲引发冷撕裂,导致焊点连接失效。
(3)焊点空洞与强度下降
盘中孔可能推挤焊锡形成空洞,减少有效焊接面积,削弱机械强度,甚至引发焊点间短路等可靠性问题。
(4)制造成本与工艺限制
盘中孔需搭配树脂/铜浆塞孔或埋盲孔工艺,相比传统过孔成本增加30%-50%。未采用特殊工艺的盘中孔表面不平整,易残留助焊剂污染。
(5)设计灵活性受限
普通盘中孔需避开密集布线区域,在高频或高速信号场景中可能因阻抗突变引发信号反射,需额外增加阻抗匹配设计。
虽然目前嘉立创能提供盘中孔工艺的能力,但是在实际项目过程中还是要考虑成本和未知的风险问题(除非经过大量的正规的验证测试)。核桃本人是比较建议在大批量项目中尽量采用外出引线打孔会较为稳妥些。
盘中孔的主要优势:
(1)布线优化与空间节省
释放布线密度:在焊盘内直接打孔可减少传统扇出过孔的绕线需求,尤其适用于细间距BGA、QFN等高密度封装,释放表层布线空间,提升PCB集成度。
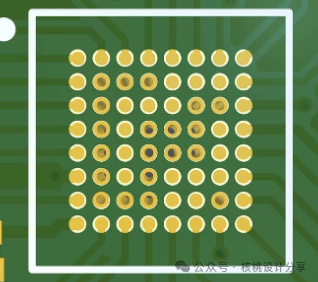
(2)简化复杂设计
通过盘中孔直接连接内层或底层,避免多层板中长距离绕线,缩短信号路径并减少线宽限制。
总结:
一:允许使用盘中孔的情况
(1)采用树脂/铜浆塞孔工艺
通过树脂或铜浆填充过孔并电镀盖帽,可避免漏锡问题,表面平整不影响焊接质量。此类工艺适用于BGA、QFN等高密度封装,能节省布线空间并提高设计灵活性。
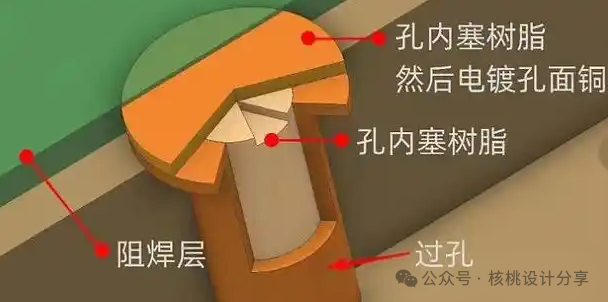
(2)使用埋盲孔(非通孔)
埋孔(内层)和盲孔(表层到内层)不会穿透整个PCB,因此不会漏锡,适合需要焊盘打孔但需避免焊接问题的场景。但此类工艺成本较高。
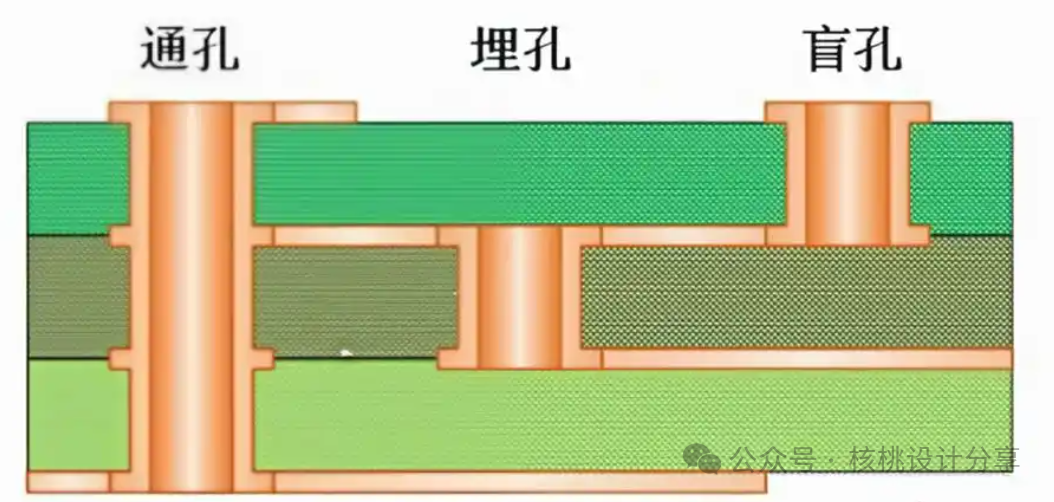
(3)散热焊盘或非焊接区域
若过孔位于芯片散热焊盘等无需焊接的位置(如中间接地焊盘),可直接打孔以增强散热或电气性能,无需特殊处理。
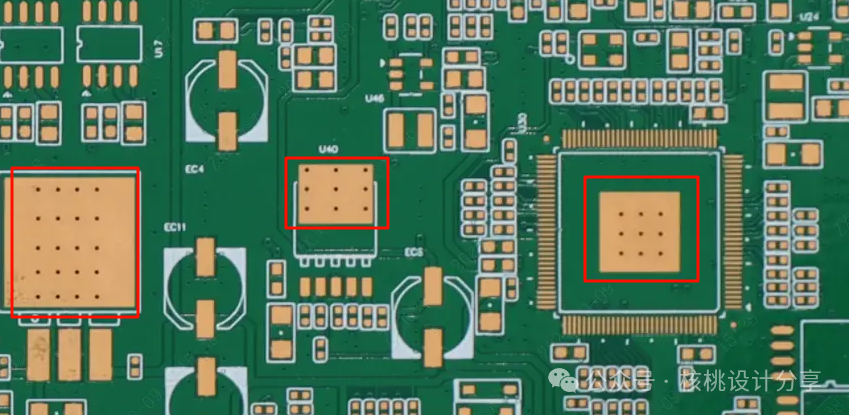
二:不建议使用盘中孔的情况
(1)普通通孔未做塞孔处理
未填充的通孔可能导致焊膏漏入孔内,造成焊盘锡量不足,引发虚焊、脱焊或“立碑”现象,尤其在小封装元件(如0402电阻)中风险更高。
(2)低成本或传统工艺场景
若PCB厂未提供塞孔工艺,或设计对成本敏感,建议采用传统扇出过孔(从焊盘外引出过孔),避免焊接风险。
最后:
盘中孔的使用需权衡工艺支持、成本、焊接可靠性及设计需求。采用塞孔技术或埋盲孔时,盘中孔是可行方案;否则应优先选择传统扇出过孔以规避风险。