隔离型双向DC-DC变换器作为储能装置与直流母线的连接桥梁,在直流微电网、电动汽车V2G充电等储能领域被广泛应用。在实际应用中根据实时工况需要,高压直流母线可通过双向DC-DC变换器对电池充电,电池也可反向对直流母线放电,从而缓解新能源发电的间歇性和波动性。在电动汽车V2G充电领域,电池的能量可通过DC-AC变换器与电网互动,实现对电网电压的削峰填谷。因此,研究1种能够进行高效率双向功率传输且电压等级较高的隔离型双向DC-DC变换器具有重要意义。
双向LLC谐振变换器可实现输入侧、 输出侧开关管的零电压ZVS( zero voltage switch )开通及输出侧开关管的零电流ZCS( zero current switch )关断,使变换器在谐振频率处具有较高的传输效率。但是, 传统双向LLC谐振变换器由于其高频区增益对频率的变化平缓,难以工作在低增益区,而大幅增加开关频率会使变换器开关损耗、 变压器及电感铜损等增大,使二次侧开关管失去ZCS关断能力,从而使变换器传输效率大幅降低。对此,可以使用多种多谐振拓扑, 利用LC器件发生串联谐振与并联谐振的原理, 通过合理地设计参数使变换器在较窄的频率范围内实现高增益特性, 并可利用3次谐波进行功率传输, 在高频段提高变换器效率; 也可将多谐振结构在一次侧引入辅助电感后应用到双向多谐振变换器中, 但是由于拓扑为两电平全桥变换器,难以满足高直流母线电压的需求;针对三电平混合钳位半桥结构,在二次侧添加1个LC谐振电路使谐振腔正、 反向结构对称, 三电平大大减小了变压器高压侧的开关管电压应力。
综上所述, 本文提出1种三电平双向全桥多谐振DC-DC变换器拓扑。该拓扑具有以下优点:直流母线侧三电平混合钳位结构可实现高压侧内管与外管的电压自均衡; 采用改进的同步变频控制策略配合附加电感,可实现所有开关管全范围ZVS开通。谐振腔多谐振结构可实现高增益,使电池侧具有较宽的电压调节范围, 可利用电流基波与3次谐波同时进行功率传输, 从而提高系统在高频段的传输效率。以下将详细分析了该拓扑的工作原理,推导出增益表达式, 讨论关键参数对变换器性能的影响,并给出了设计原则。
1、拓扑结构及正反向工作原理
图1为三电平双向全桥多谐振DC-DC变换器拓扑结构, 其高压直流母线侧采用三电平全桥混合钳位结构; 谐振腔在LLC结构的基础上添加辅助电感Lm2,并在谐振电容Cp两端并联1个LC谐振电路,构成新型谐振腔结构;低压电池侧采用两电平全桥结构。
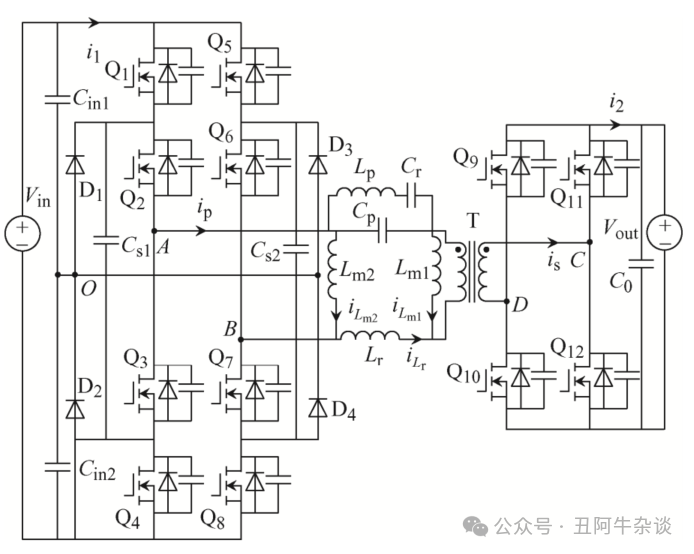
图一、三电平双向全桥多谐振DC-DC变换器
当变换器正向工作时, 根据其工作频率可分为f
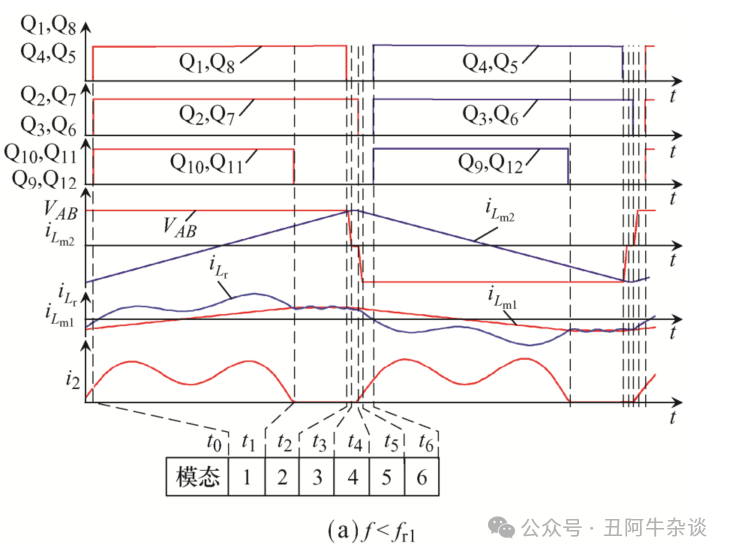
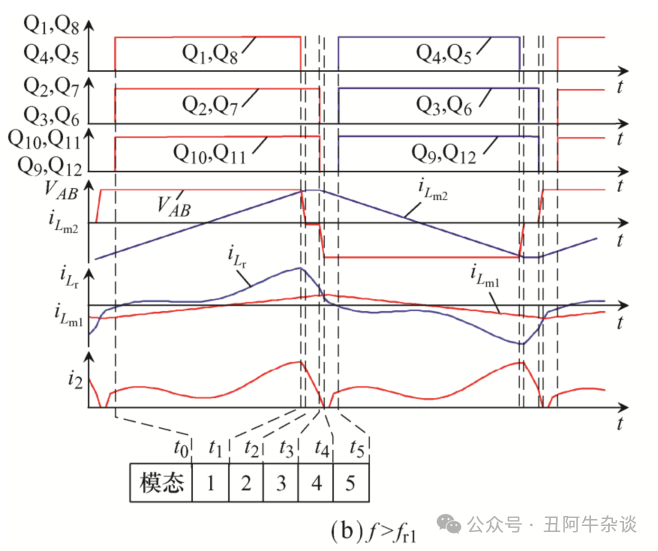
图2、变换器正向工作波形
改进的同步变频控制策略是指当f
模态1 [t0,t1]:t0时刻,高、低压侧正半桥臂开关管同时导通,变换器由正半桥臂从高压侧向低压侧传输功率,VAB在桥臂开通前上升至Vin,辅助电感电流iLm 2在VAB作用下线性上升。 由于励磁电感Lm1被二次侧钳位不参与谐振,因此谐振腔元件Lp、Cp、Lr、Cr共同谐振使谐振腔电流iLr呈“馒头波”形状上升。
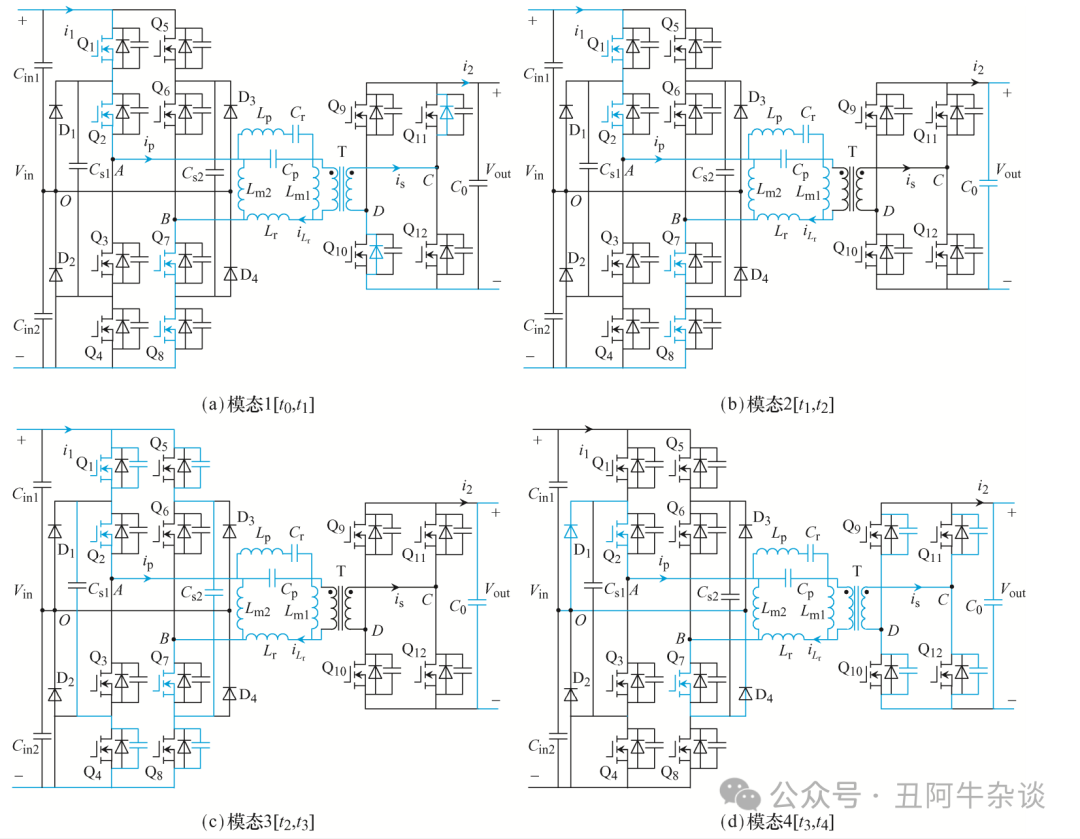
图3、f
模态2 [t1,t2]:由于f
模态3 [t2,t3]:t2时刻,关断高压侧正半桥臂外管Q1、Q8,高压侧电流i_p(i_p = i_{L_r} + i_{L_m} ) 对外管Q1、Q8的寄生电容进行充电,同时Q4、Q5的寄生电容通过飞跨电容Cs1、Cs2放电。
模态4 [t3,t4]:t3时刻, 高压侧外管寄生电容充、放电完成,VAB下降至0,但高压侧电流ip未下降至0,钳位二极管D1、D4提供续流路径。同时,励磁电感与谐振腔谐振结束后,由于iLr下降较快, iL
模态5 [t4,t5]:t4时刻,关断高压侧正半桥臂内管Q2、Q7,高压侧电流ip通过飞跨电容Cs1、Cs2对内管Q2、Q7的寄生电容进行充电,对Q3、Q6的寄生电容放电。低压侧开关管Q10、Q11完成充电后,由Q9、Q12的寄生二极管提供流通路径,高压侧继续向低压侧传输功率,i2开始上升。
模态6 [t5,t6]:t5时刻,VAB下降至-Vin,高压侧电流ip通过Q3、Q4、Q5、Q6的寄生二极管续流,向低压侧传输功率,t6时刻高压侧与低压侧负半桥臂开关管实现ZVS开通。
由图2( b )可以看出,当f>fr1时,由于开关周期小于谐振周期, 低压侧开关管与高压侧内管同时关断,低压侧电流is在t4~t5之间过零变负,从而低压侧可实现ZVS, 但很明显低压侧开关管失去ZCS关断,其余工作模态与f
2、拓扑增益特性分析
在变频控制方式下对三电平双向全桥多谐振拓扑工作特性, 主要是在不同开关频率时的增益特性进行分析。 三电平双向全桥多谐振变换器谐振腔简化模型如图4所示,其中Re为变换器低压侧等效到高压侧的负载。可见,由于辅助电感Lm2的加入,使得谐振腔等效电路左右对称,故仅需对其中1个方向进行分析。当陷波器Lp、Cp、Cr发生并联谐振时,其阻抗为无穷大,可使变换器增益为0;当谐振腔Lp、Lr、Cp、Cr发生串联谐振时,其阻抗为0,使变换器增益为1。据此可以得到陷波器频率frp与谐振频率fr1、fr2的表达式分别为
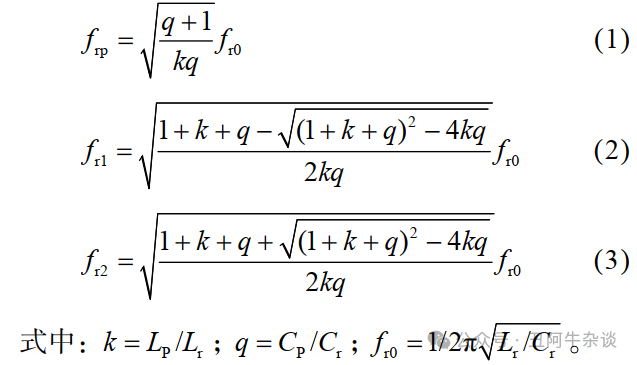
可以看出,陷波器有2个串联谐振频率和1个并联谐振频率,而方波经傅里叶分解后含有逐次衰减的奇次谐波,故可设定fr2=3fr1,可使变换器同时利用基波电流与3次谐波电流进行功率传输。同时,为了使变换器在小频率范围内具有宽电压增益特性,可将陷波器频率frp设定在fr1与fr2之间。
多谐振变换器谐振腔增益M为
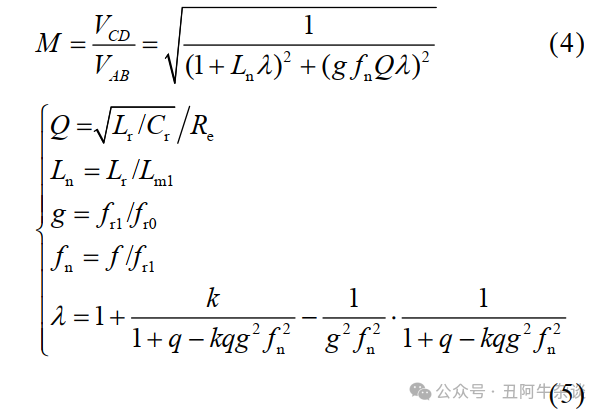
式中,fn为归一化频率。在MATLAB中绘制变换器增益随fn变化的曲线,如图5所示,其中fr1n、fr2n与frpn分别为归一化的第1谐振频率、第2谐振频率与陷波器频率。在图5的虚线左侧区域Ⅰ内,变换器增益随频率的增大而增大,为容性区,此区域无法实现开关管的ZVS开通;虚线右侧区域Ⅱ为升压区域,区域Ⅲ为f >fr1降压区域,区域Ⅱ与区域Ⅲ为感性区域,是变换器的理想工作区域,可实现ZVS导通。由图5可以看出,随着负载的加重,Q将增大, 变换器将更容易进入容性区。 同时,由于设定fr2=3fr1,在3次谐波处也存在电压增益,能够传递3次谐波功率。
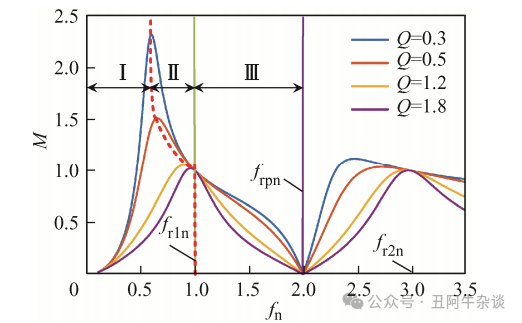
图5、变换器增益曲线
3、变换器关键参数设计
由变换器的归一化增益公式( 4 )可知, 增益大小除了与开关频率有关,还与k、q、Ln、Q这4个参数有关,故变换器参数设计将从效率与增益需求2个角度考虑,主要对k、q、Ln、Q这4个参数进行设计。以2 kW实验样机为例,正、反向运行技术指标见表1。
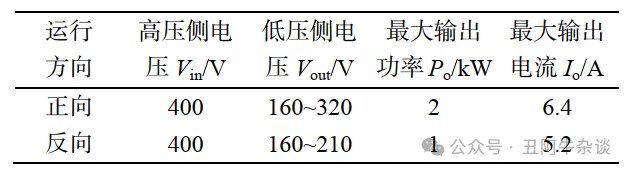
表1、正、反向运行技术指标
3.1、谐振网络设计
以
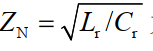
为标准阻抗,对变换器陷波器阻抗

与谐振腔阻抗
进行归一化简化,可得
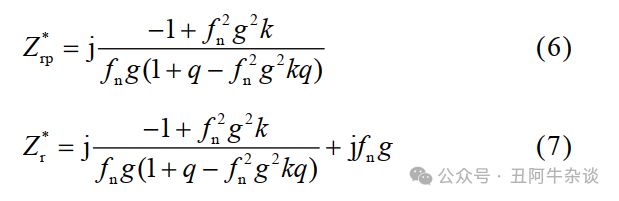
故k和q会影响陷波器阻抗及谐振腔阻抗的大小,谐振频率与陷波器频率的位置与其取值有关,设定fr2=3fr1、frp=2fr1,由式( 1 )~式( 3 )可求得k=2.4,q=0.6。
三电平双向全桥多谐振拓扑可实现高、 低压侧所有开关管的ZVS开通, 故对变换器进行损耗分析时仅考虑关断损耗及谐振腔环流损耗。 这2项损耗除了与系统开关频率有关外, 还与高压侧开关管关断损耗和高压侧电流ip( off )有关, 与谐振腔环流损耗和电流iLr有关,损耗与电流大小成正比。由式( 5 )可知,Q和Ln的取值分别与励磁电感和负载的取值有关, 故二者在影响变换器增益的同时也必然影响变换器损耗。
在系统开关频率为第1谐振频率(f=fr1)处进行分析,此时谐振腔Lp、Cp、Lr、Cr谐振频率等于系统开关频率, 励磁电流与辅助电感电流在整个周期内线性变换,假设Lm1=Lm2=Lm,且高压侧开关管开通与关断时励磁电感电流 与谐振腔电流 相等,则有
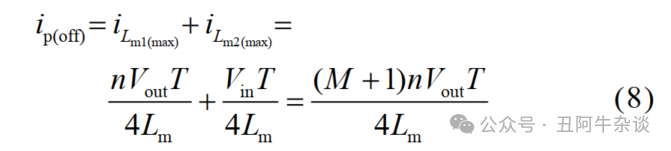
式中:ip( off )为外管Q1、Q8关断时变压器一次侧电流; iLm1(max)为励磁电感的最大电流;iLm2(max) 为辅助电感的最大电流;n为变压器变比;T为开关周期。
变换器工作时, 谐振腔电流大小主要为电流基波与3次谐波分量叠加,可表示为
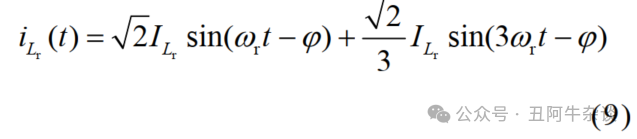
式中:ILr为谐振腔电流有效值;ωr为fr1对应的角频率;φ为高压侧电压超前电流的相角。由
riL(0)=-iLm1(max)可得

1/2个周期内,谐振腔电流平均值等于励磁电感电流与变压器高压侧电流之和,即

故求得谐振腔电流有效值为

以变压器高压侧电流
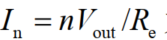
为基准,对电流Ip( off )与 ILr进行标幺化,可得
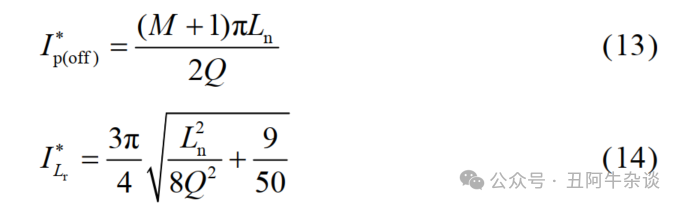
故导通损耗和关断损耗均与Ln呈正相关,与Q呈负相关。变换器的参数设计在满足增益条件的同时,Ln应尽可能小,Q应尽可能大。
3.2变换器参数设计
由图5可见,在相同频率下,变压器的增益随负载的增大而减小, 故在满载情况下有最低输出电压,在空载情况下有最高输出电压。要使设计的变换器满足增益调节范围, 则在满载情况下开关频率最小处的输出电压应大于变换器的最大期望输出电压;在空载情况下,开关频率最大处的输出电压应小于变换器的最小期望输出电压。
综合考虑系统的功率、体积及损耗等因素,取高压侧电压为400 V,第1谐振频率fr1=100 kHz,第1谐振频率处低压侧输出电压为200 V,可设计变换器变比为2,故谐振腔最大增益Mmax=1.6,最小增益Mmin=0.5。
首先在空载(Q=0 )情况下由Mmin确定变换器参数Ln。图6为变换器增益随fn与Ln变化的三维曲面与Mmin<0.8在平面上的投影。 在满足增益需求的前提下,为保证更窄的频率调节范围及更小的损耗,综合考虑后取Ln=0.14。Ln确定后,将其代入增益公式,以fn和Q为变量绘制增益的三维曲面与Mmax>1.6在平面上的投影,如图7所示,根据设计需求,取Q=0.5。
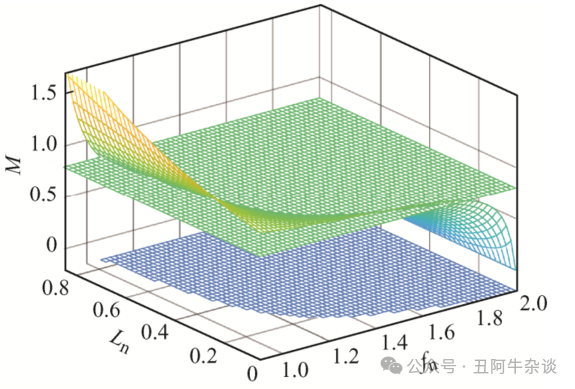
图6、增益M随fn与Ln变化曲面
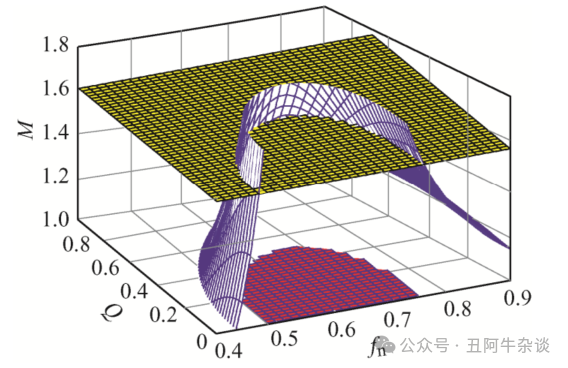
图7、增益随fn与Q变化曲面
谐振频率与谐振网络归一化参数k、q、Ln、Q确定后,谐振网络参数大小可由
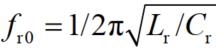
再结合式( 4 )和式( 5 )求得,此处不再展开。
4、实验验证
为验证上述理论分析及参数设计的合理性,本文搭建2 kW实验平台,变换器关键参数见表2。
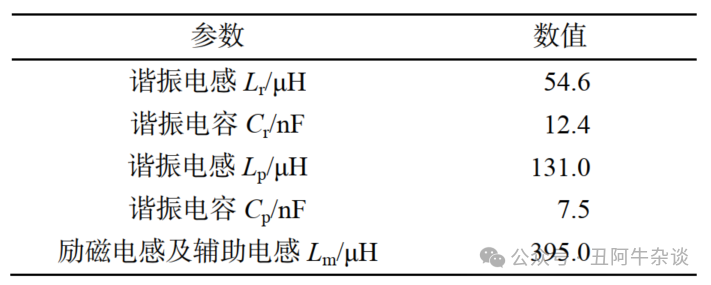
表2、多谐振变换器主要技术参数
4.1、正向实验验证
图8为开关频率72 kHz(即f
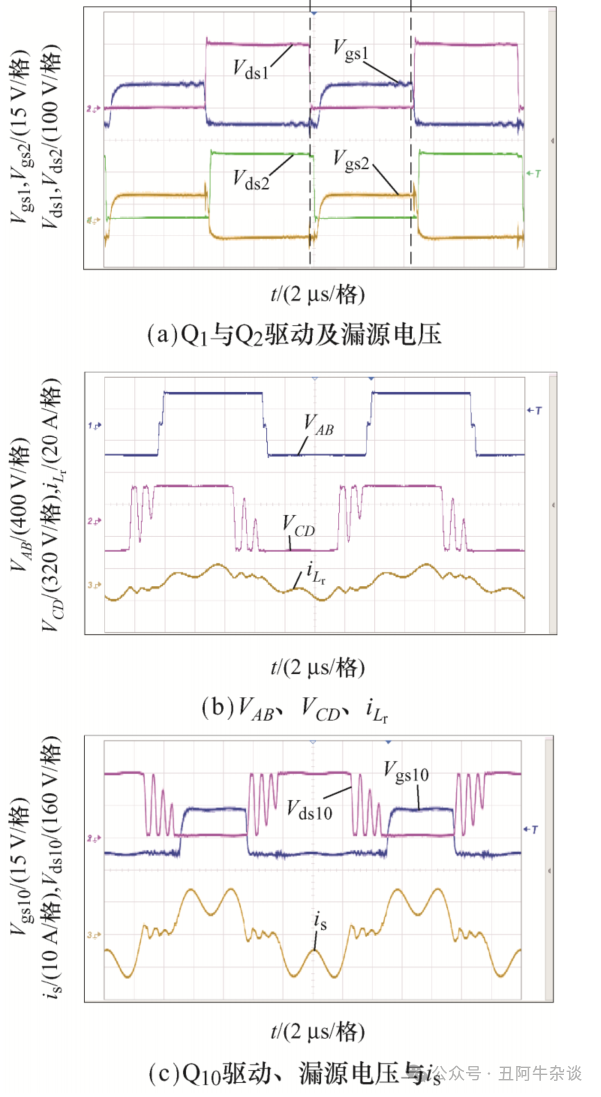
图8、f
图9为开关频率125 kHz(即f>fr1)、低压侧输出电压160 V、输出电流6.4 A时的关键波形。由图9( a )可见,Q1与Q2同样实现了ZVS开通;由图9( b )可以看出, 由于此时开关管开关周期小于谐振腔谐振周期, 高压侧开关管在谐振周期结束前关断,低压侧电压VCD在谐振电流iLr降为0时,由正变负;由图9( c )可以看出,Q10实现了ZVS开通,但关断时低压侧电流is未下降至0, 未实现ZCS关断。
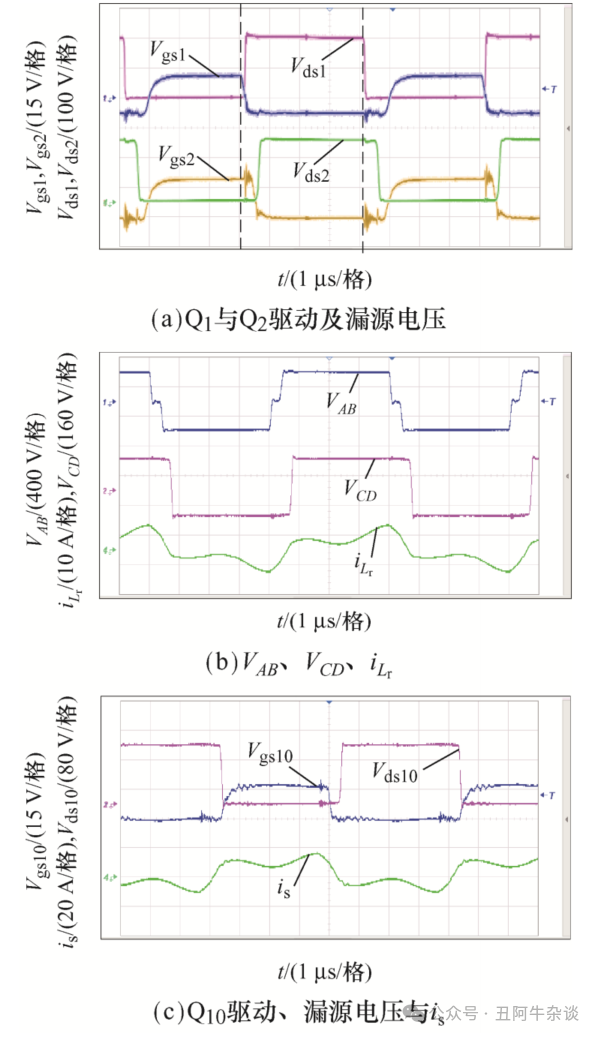
图9、f>fr1时正向工作的关键波形
4.2、反向实验验证
图10为开关频率75 kHz(即f
图11为开关频率120 kHz(即f>fr1)、高压侧输出电压400 V、低压侧输入电压210 V时的关键波形。由图11( a )可以看出,高、低压侧桥臂同样可实现ZVS开通。
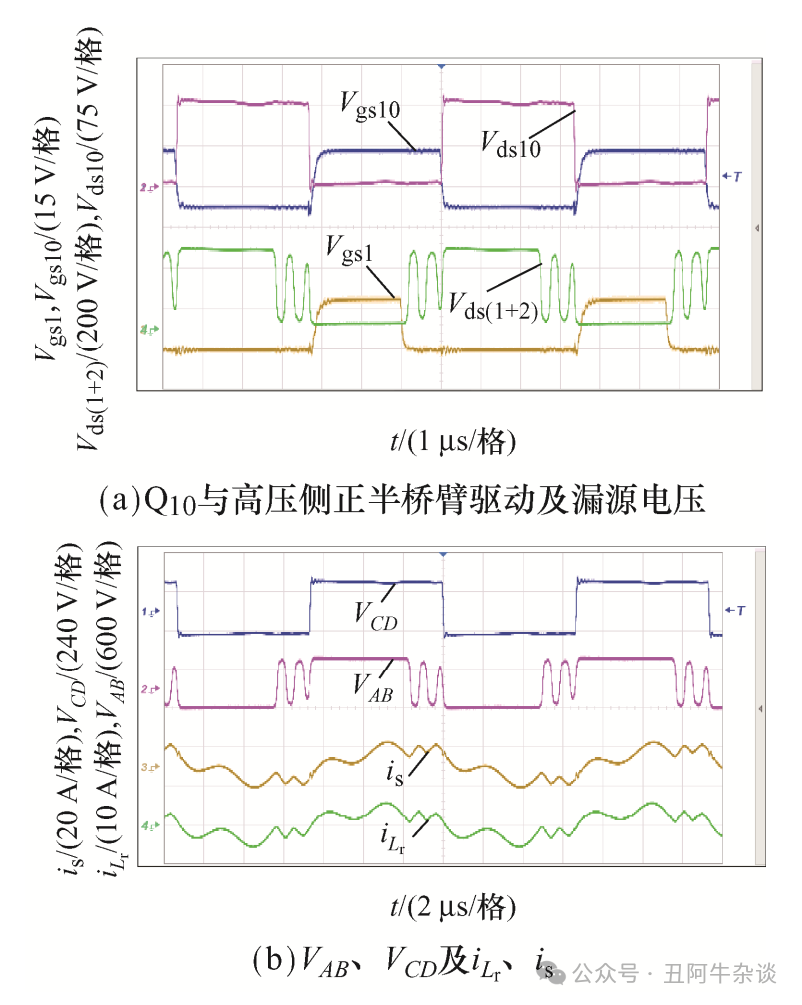
图10、f

图11、f>fr1时反向工作的关键波形
4.3、实验效率
采用相同的参数设计方法, 在相同指标要求下设计添加辅助电感的三电平双向LLC谐振变换器,主要参数见表3。本文设计变换器Q=0.57、Ln=0.34,与LLC变换器相比,Q相相差不大,但Ln相相差较大。该LLC变换器可在72~138 kHz频率范围内实现160~320V的2倍电压增益,与多谐振变换器相比,工作频率范围更大。
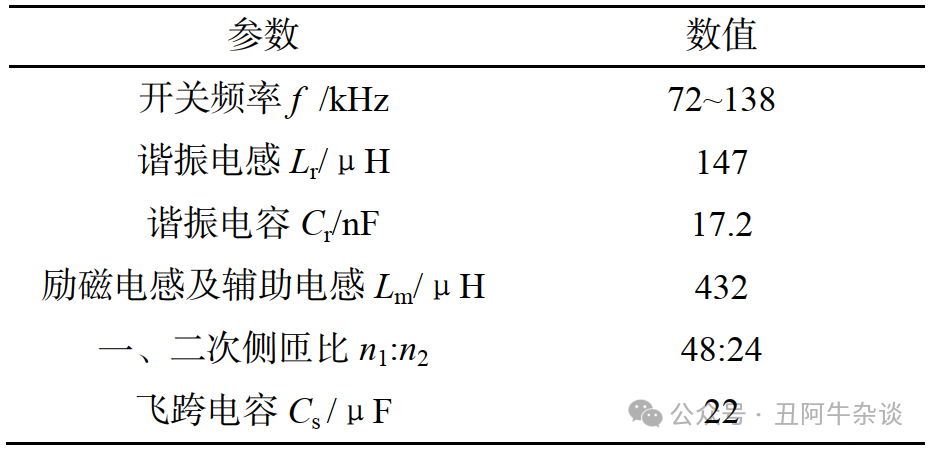
表3 LLC变换器主要技术参数
图12为变换器正向运行低压侧以6.4 A恒流输出时,三电平双向全桥多谐振变换器与三电平双向全桥LLC变换器的效率对比曲线。可以看出: 多谐振变换器在谐振频率点有1.28 kW输出,此时效率最高达到96.9%;峰值效率右侧f
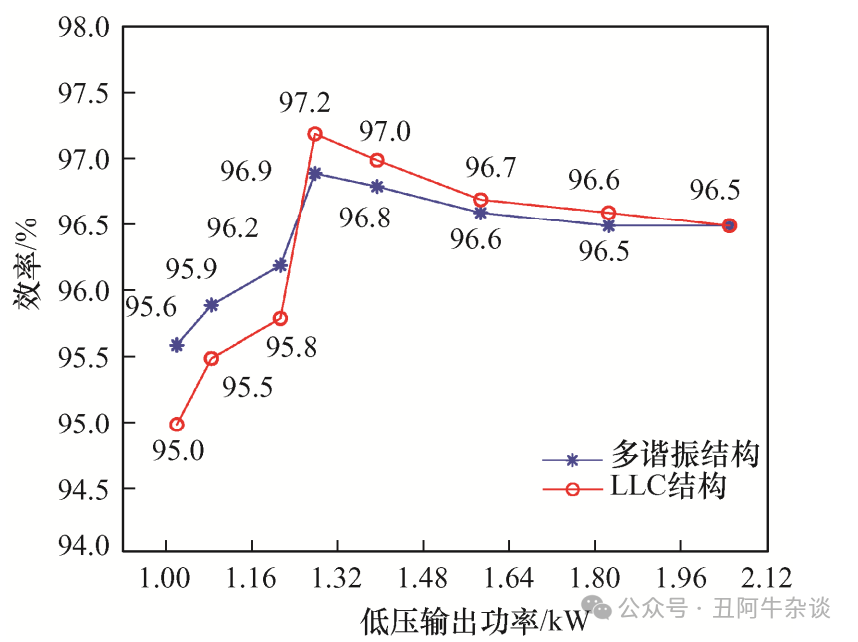
图12、正向效率对比
5、结论
该拓扑采用改进的同步变频控制策略,在实现高压侧桥臂内、 外管电压自均衡的同时具有更宽的电压调节范围。通过2kW系统平台实验得到如下结论。
(1)系统正、反向运行均可实现开关管的ZVS,同时可利用3次谐波进行功率传输减小功率损耗。
(2)变换器正向工作时, 在72~125 kHz频率变化范围内即可实现低压侧160~320 V的2倍电压增益;反向工作时,当低压侧160-210V输入时可在75-120 kHz频率变化范围内使高压侧输出400V,即在较小的频率变化区间可以获得较大的增益范围。
(3)多谐振变换器正向峰值效率可达96.9%,与LLC变换器相比,在f
f>fr1范围内效率有明显提升,表明所提多谐振变换器有益于提高变换器的整机效率。