摘要:
铜基镀银引线框架作为半导体封装的主要材料之一,其铜面和镀银区易受空气影响造成化学腐蚀,随着时间的变长,此种化学腐蚀程度会不断增加。由于化学腐蚀过度会造成引线框架表面的可焊性降低,最终造成焊线脱落和封装后分层问题,故铜面和镀银区的表面状态对半导体的可靠性有重要影响。本文介绍了铜基镀银引线框架生产过程中不同电镀工艺和铜保护剂类型的差异性,提出了铜基镀银引线框架生产过程中抗化学腐蚀性实现的关键控制点,为引线框架产品可靠性的提升预防提供数据支持。
0 引言
在生产和使用过程中,如果对引线框架保护不当,其表面容易与氧气或硫化物发生化合反应形成组织疏松的变色层;由于该层过厚会降低其与封装树脂之间的结合强度,导致封装树脂和引线框架之间有纳米级的分层和开裂现象,最终出现可靠性问题[1-2]。为了减少分层风险,引线框架设计时会增加锁胶孔、圆形凹孔、半蚀刻区域和表面粗化等方式[3]。其中,铜面和镀银区的表面状态对半导体的可靠性有重要影响:
(1)引线框架铜面变色的主要原因。其是由于铜与 氧 气 反 应 生 成 氧 化 铜 (CuO)和 氧 化 亚 铜(Cu2O),CuO 呈黑色,Cu2O 呈红色,这些氧化物会使基材铜进一步氧化[4],使引线框架表面的金属氧化物结合力下降,从而影响树脂和氧化区的结合。相关数据显示,当塑料方型扁平式封装 LQFP64 的 1.4mm厚度的封装体氧化层厚度的增长到 42.5nm 时,封装体会发生分层和开裂的情况[5-6],为了避免铜面氧化,通常会在引线框架表面浸润一层铜保护剂。
(2)引线框架镀银变色的主要原因。其是由于镀银层遇空气中的硫化物反应生成硫化银和氧化银。银对大气环 境 中 微 量 的 硫 化 氢(H2S)很 敏 感 ,H2S 浓度 为0.3μg/m3 时,足以引起银的硫化变色[7-8]。单质镀银层暴露于空气中与含硫、硫氧化物、卤化物等接触,易生成氯化银 (AgCl)、硫酸银 (Ag2SO4)、硫化银(Ag2S)等难溶物质,致使银层失去原先的光泽,逐渐变成浅黄色、黄褐色的薄膜,同时会导致导电、导热和焊接等性能降低[9-11]。
本文对镀银引线框架不同电镀工艺对镀银区品质、铜保护剂类型的影响研究,获得镀银引线框架抗化学腐蚀性的最优工艺和使用方案。
1 引线框架制程介绍
引线框架按成型工艺可以分为模具冲压法和化学刻蚀法[12],典型的模具冲压法和化学刻蚀法的工艺流程如图 1 所示。
另外,引线框架电镀生产流程如图 2 所示。其中,预备处理工序(Pre-Treatment)主要是对镀银前的基材表面进行清洁,确保镀银和基材表面的结合性,包括预镀铜工序(Cu Strike)和防置换工序(Anti-Immersion)。镀银工序(Ag Plating)主要使镀银层表面结晶均匀、具有高耐热性和低硬度,从而保证较高可焊性。后处理工序(Post-Treatment)主要对引线框架进行表面保护,包括抗氧化工序(Anti-Oxidant)和防银胶扩散工序(Anti-EBO)。
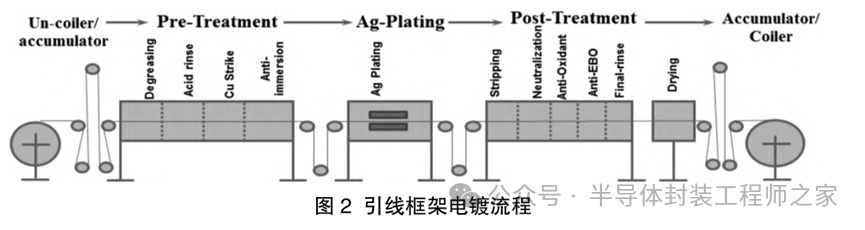
2 生产过程对引线框架抗化学腐蚀性的影响
2.1 镀银对引线框架抗化学腐蚀性的影响
2.1.1 喷镀和浸镀的差异
氰化银钾(KAg(CN)2)是电镀液的主盐成分,提供电沉积所需的离子[13]。由于环保要求和无氰镀银稳定性不理想,大部分工厂会选用低氰高速电镀的方式进行镀银,故目前仍以氰化体系占主导地位[14]。常见的引线框架镀银方式分为两种,一种是喷镀银,另一种是浸镀银,这两种工艺重要参数如表 1 所示,从中看出:喷镀工艺使用较高的镀银温度和电流密度,当电流在短时间内增加,而镀液配位能力较弱时,晶体快速成核与生长[15],电流密度高,需配合较高的氰离子(CN-)浓度,才可以减少晶粒的过度生长;当电流密度降低时,镀银温度窗口减小。因此,镀银电流需符合引线框架电镀的电流密度和温度范围[16-17]。
图 3 是 A194 铜基镀银引线框架浸镀产品和喷镀产品镀银区的 50000 倍扫描电子显微镜(SEM)形貌图,可以看到:①喷镀银面致密性好,晶粒均匀且直径约 2um。②浸镀银面晶粒粗糙且直径约 8um,产生的镀银层晶界明显。应该看到,如果喷镀工艺在极短的时间内一次性完成,即速度在 3~4 秒 / 条,并且Ag+ 的浓度会较浸镀溶液高, 而 CN- 浓度也相对高,则此时的镀液配位能力较强,获得镀银的晶粒度更小。而且,电镀温度较高,镀银层组织更均匀[14];如果浸镀工艺是以 6~7 秒/ 条的速度通过 4~6 个镀银缸体,则每个缸体中的杂质离子会在镀银区进行沉积,使镀银结构相对疏松且不平整。
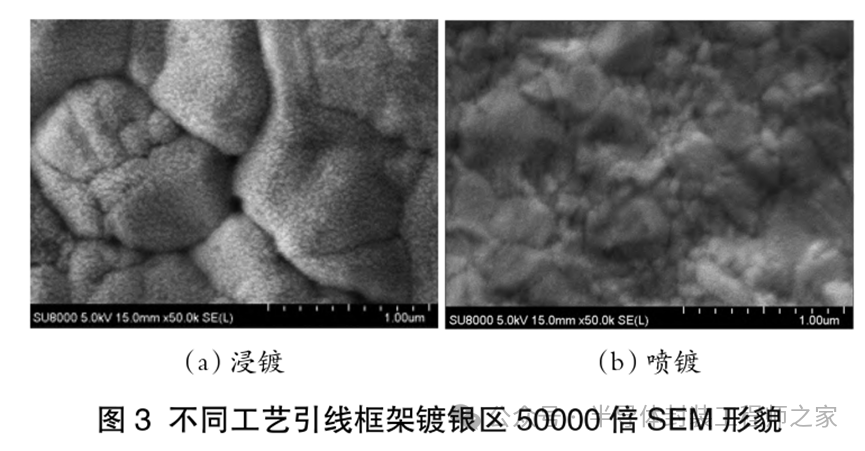
我们选取六款 A194 铜基镀银引线框架,在含有相同硫化物浓度的环境下进行放置实验,使用光学显微镜观察引线框架镀银区化学腐蚀变色的情况。镀银层表面的规格按 GB/T 15878-2015《半导体集成电路小外形封装引线框架规范》要求,镀层表面应致密、平滑、色泽均匀呈镀层本色,不允许有起皮、起泡、沾污、斑点、水迹、异物、发花等缺陷。从表 2 可以看到,浸镀样品 D、E、F 样品在室温 48 小时放置后会发生变色现象,而喷镀样品 A、B、C 在室温 72小时放置后无变色现象。
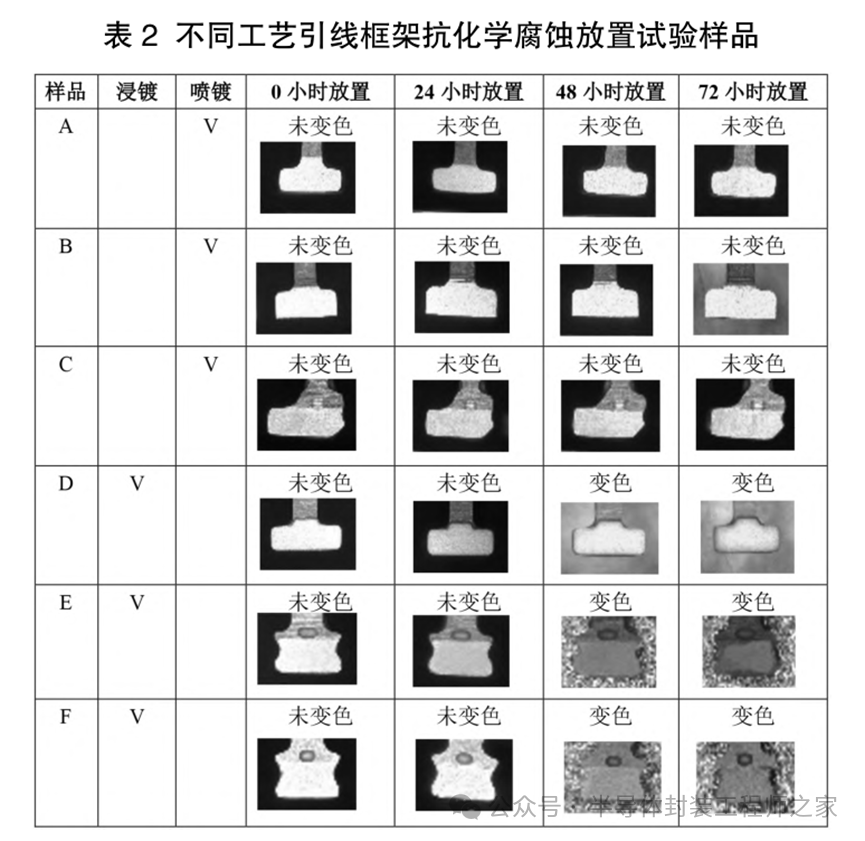
同时,采用日本日立光谱仪(HITACHI Horiba)进行能量色散 X 射线(EDX)分析,获取镀银表面的元素差异,如图 4 所示:镀银区变色有 S 和 O 元素的存在,浸镀银区发生了硫化反应。
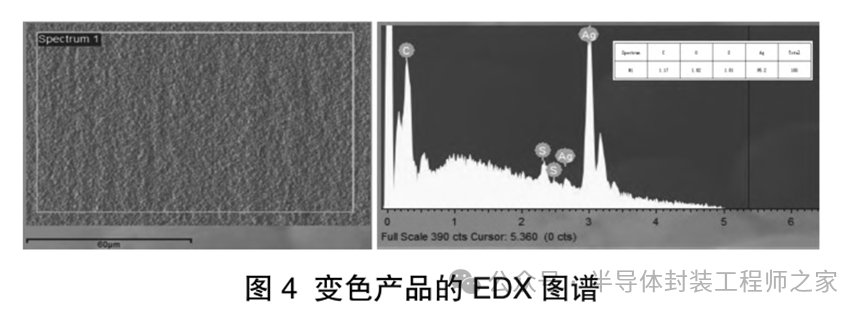
实验表明,浸镀工艺的产品镀银区抗化学腐蚀性较弱,而喷镀工艺的产品镀银区抗化学腐蚀性持久时间较长。其主要原因是喷镀工艺的镀银致密度较高,腐蚀性的元素不易与镀银组织反应形成化学腐蚀。另外,由于表面较为平整光滑,在镀银后制程中容易清洗,镀银区含有的杂质较少,无法轻易进行腐蚀原电池反应而导致化学腐蚀。
2.1.2 镀银厚度的影响
我们 选 取 UHE2312152、UHE2311272和UHE2308242 的不同镀银厚度的 A194 铜基镀银引线框架产品,放置在含有硫化物的同一固定环境中,采用 HITACHI Horiba 进行 EDX 分析镀银变色层表面硫含量分析,获得不同厚度与硫含量的关系,如表3 所示。
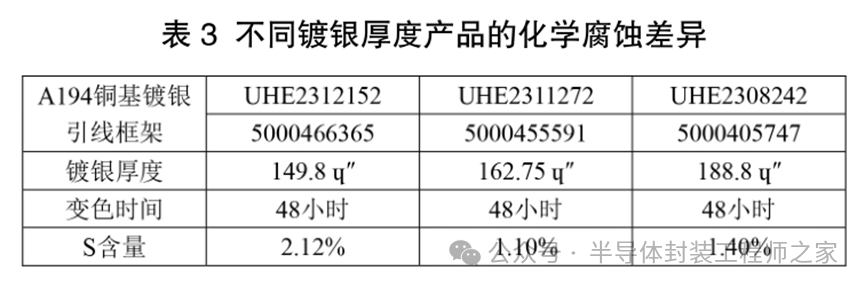
实验表明:这三款不同镀银厚度的镀层在 48 小时后都有变色现象,硫元素含量和镀银厚度无线性关系。相同镀银工艺的产品,不同镀银厚度对引线框架的抗化学腐蚀性能影响不显著。
2.2 铜保护剂对引线框架抗化学腐蚀性的影响
从“前线分子轨道理论”分析有电子得失的氧化- 还原反应,本质上是还原剂分子最高占有轨道(HOMO)与氧化剂分子的最低空轨道(LUMO)因能级(E)差较大产生电子转移发生氧化 - 还原反应[18]。且铜保护剂大多是有机物,主要呈电负性。目前,第一代铜保护剂为有机硫化合物或氮烯化合物,如图5(a)所示,有机硫化合物被同时吸附在银和铜表面,而氮烯化合物只吸附在铜表面,因此硫系的保护剂较普遍应用在框架镀银上;第二代保护剂是含硫无机物保护剂,如图 5(b)所示,无机保护剂不但具有良好的有机膜防变色效果,同时适用于高热冲击的应用(300℃左右)。图 5 显示了以有机物铜保护剂为例的作用机理。从中看出:①其是以碳链为载体,铜保护的官能团 R1、R2 作为抗氧化功能实现的基团,通过碳链和引线框架表面络合,以达到改变其电荷分布和状态的目的,可使金属表面的能量更平稳,腐蚀速率放缓[19]。②官能团的有机链的组合形式不同,其抗氧化能力也不同。
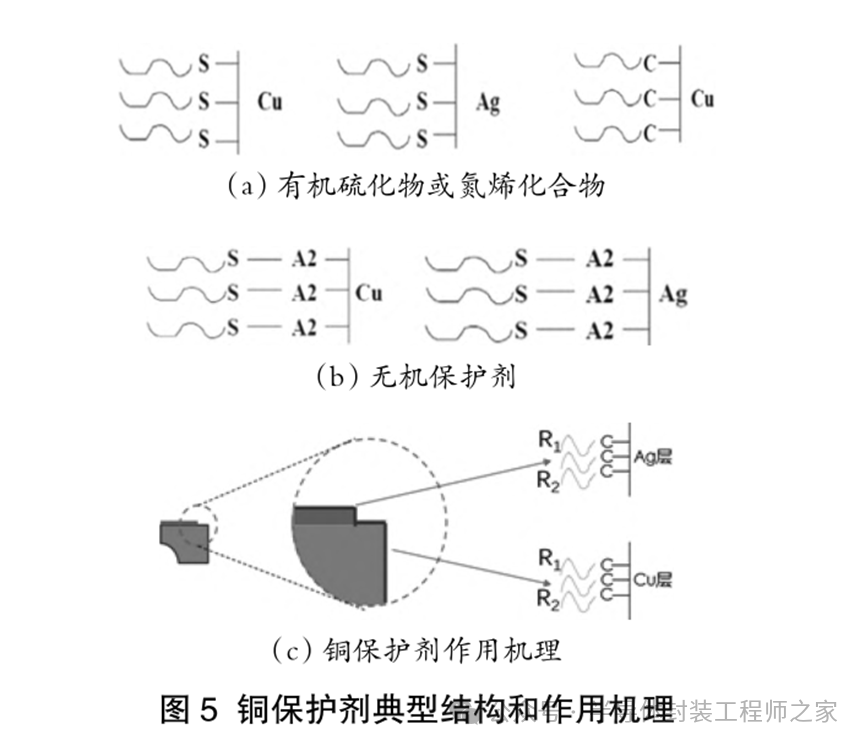
2.2.1 铜保护的成分差异
传统的防变色处理为六价铬酸盐钝化和苯并三氮唑(BTA)钝化两种。其中,六价铬酸盐因其有强氧化性在铜表面形成钝化层, 铜钝化后电极电位向正方向移动,改变了铜表面的双电层结构,从而使电极电位发生了相应的变化,降低金属表面的氧化速度。另外,有机铜保护剂通常为含氮和含硫的杂环化合物,如苯并三氮唑 (BTA)、和 2- 巯基苯并噻唑(MBT)等,可以在氧化亚铜表面形成致密的 Cu(I)配合物膜,即 BTA-Cu 络合物膜。Cu(I)容易与含硫的缓蚀剂形成稳定的配位键,能承受 200℃以上的热振动[20]。
我们选取不同类型铜保护剂对 A194 铜基引线框架进行烘烤及铜剥离测试,按 GB/T 15878-2015《半导体集成电路小外形封装引线框架规范》要求执行。A、B、C 三款产品在 230℃烘烤 10 分钟后铜剥离测试全部通过,药水 A 和 B 为有机物铜保护剂,而药水 C 添加了巯基有机物。如表 4 所示,A、B、C 三款产品在 200℃烤箱烘烤2min 后,铜保护药水 A和 B 处理的引线框架变色;而药水 C 处理的引线框架未变色,其原因为药水 C 处理过的引线框架具有最好的耐热性。
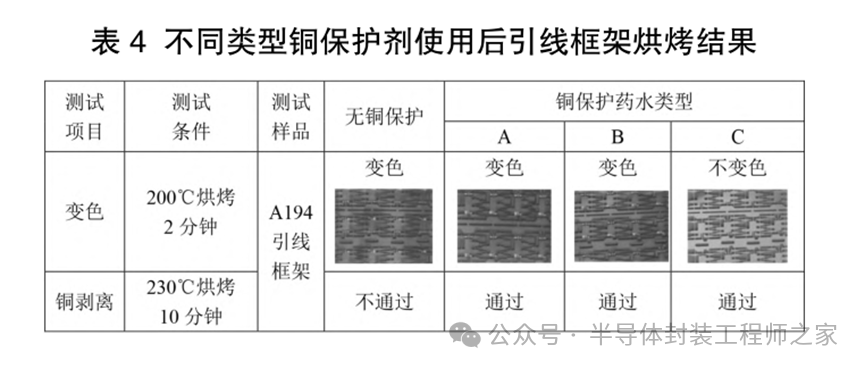
实验表明,高温型铜保护剂分子中的硫对铜的配位能力更强,它可以明显提高铜保护效果,铜保护剂会在引线框架表面形成巯基(-SH)型保护膜,吸附铜面,以对抗高温高湿环境下引线框架的氧化。
2.2.2 铜保护剂中有无银离子
当铜保护剂中加入适量银盐后,银离子会与铜表面发生置换反应,在铜面形成极薄银层,起到保护铜层和阻止铜层跃迁的作用,如图 6 所示。以 N磺胺噻唑硫代乙醇酸(STG)铜保护剂为例,起保护作用的主要原因是在镀银表面形成了(Ag+ 与 N- 磺胺噻唑硫代乙醇酸的配合物)STG-Ag 等类似的多位点配位配合物,其 N 原子和巯基均可与 Ag+ 配位形成致密的表面配合物膜,有效抑制腐蚀介质与表面的反应,表面膜的良好导电性可归因于多维共轭效应[21]。当铜保护剂成膜后电荷传递电阻大幅度增大,腐蚀介质与银电极发生氧化还原反应的电荷转移阻力增大,银发生的腐蚀难度提高[22]。
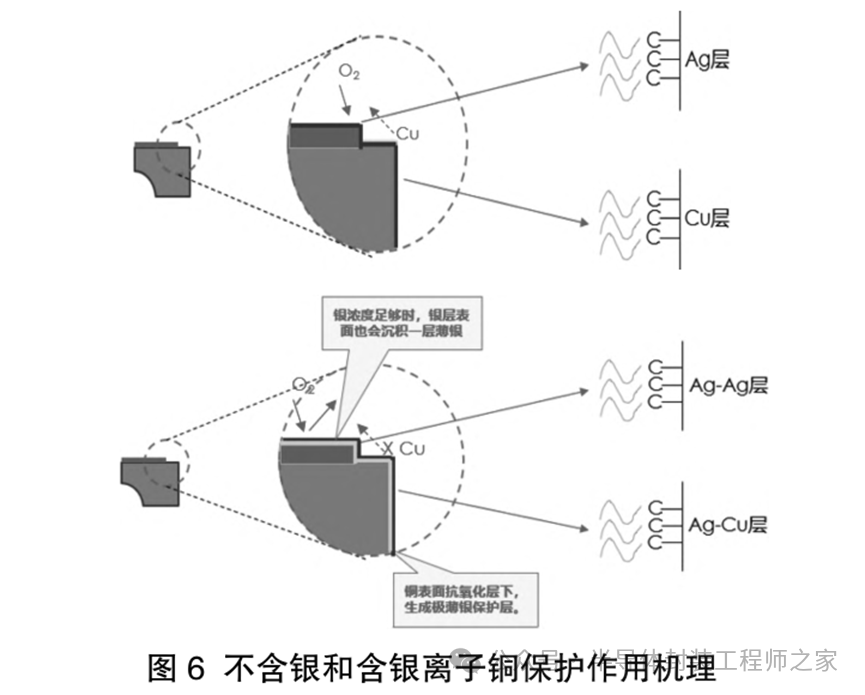
本文通过选用浓度为 5ml/L 和20ml/L 的铜保护剂浸润 A194 铜基镀银引线框架后,进行无银离子活化剂和添加银离子活化剂的前后不同温度下的烘烤试验,结果如表 5 所示。当铜保护浓度为 5ml/L时,添加银离子活化剂会提升铜保护效果;当铜保护浓度为 20ml/L 时,添加银离子活化剂与否不影响效果。通常情况下,铜保护过程中银离子活化剂的添加量在 2.7~4.2g/L 之间,在不产生锡渣的前提下,可以确保镀银引线框架的抗氧化性。
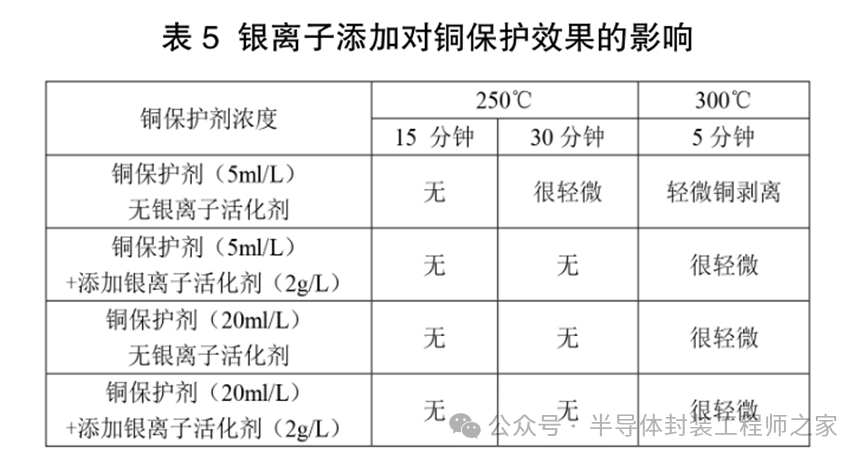
实验表明,当铜保护剂浓度较低时,添加银离子活化剂可以提升引线框架抗化学腐蚀性能;而当铜保护剂达到较高浓度时,无论是否添加银离子活化剂,都可以保证引线框架抗化学腐蚀性能。
3 结论
本文通过对引线框架的生产工艺展开研究,阐述了引线框架表面发生变色的影响因子、机理和引线框架表面保护措施。文章结合充分的实验数据及相关文献,从不同种类的镀银工艺和铜保护剂两大方面探讨铜基镀银引线框架抗化学腐蚀性能的影响。主要得到以下结论:
(1)浸镀工艺与喷镀工艺对引线框架抗化学腐蚀性能的影响
喷镀工艺由于银离子浓度较大、镀银温度高且镀银时间短,可以获得晶粒细小均匀而致密且平整无杂质的镀银层,使外界污染物与引线框架镀银面的接触面积减小,在后处理工艺或使用环节中不容易残留污染而形成化学腐蚀,从而有效提高引线框架的抗化学腐蚀性能。相同镀银工艺不同镀银厚度对引线框架的抗化学腐蚀性能影响不显著。
(2)铜保护剂类型对引线框架抗化学腐蚀性能的影响
铜保护剂中添加银离子可以提升铜基引线框架抗化学腐蚀性能,铜保护剂中添加巯基有机物对铜保护的抗高温分解性能影响显著,从而提升引线框架的抗化学腐蚀性能。