铜引线键合由于在价格、电导率和热导率等方面的优势有望取代传统的金引线键合, 然而 Cu/Al 引线键合界面的金属间化合物 (intermetallic compounds, IMC) 的过量生长将增大接触电阻和降低键合强度, 从而影响器件的性能和可靠性。 针对以上问题, 本文基于原位高分辨透射电子显微镜技术, 研究了在 50—220◦C 退火温度下, Cu/Al 引线键合界面 IMC 的生长问题, 实时观测到了 Cu/Al IMC的动态生长及结构演变过程。 实验结果表明, 退火前颗粒状的 Cu/Al IMC 分布在键合界面, 主要成分为 Cu9Al4, 少量成分为 CuAl2。退火后 Cu/Al IMC 的成分是: 靠近 Cu 一端为 Cu9Al4, 远离 Cu 的一端为 CuAl2。同时基于原位观测 Cu/Al IMC 的动态生长过程, 计算得到了 Cu/Al IMC 不同温度下的反应速率和激活能, 给出了基于原位实验结果的Cu/Al IMC的生长公式, 为优化Cu/Al引线键合工艺和提高Cu/Al引线键合的可靠性提供了指导。
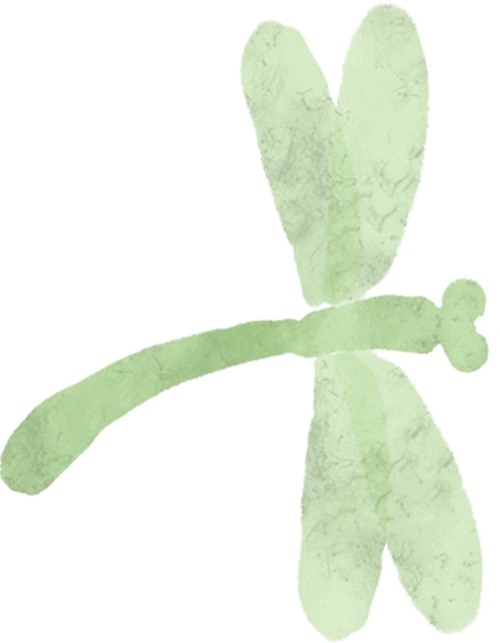
一、介绍
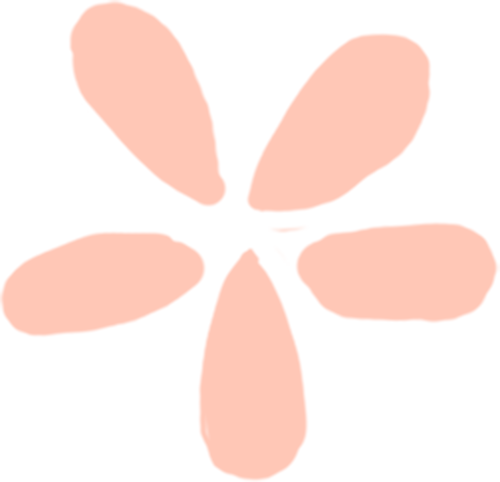
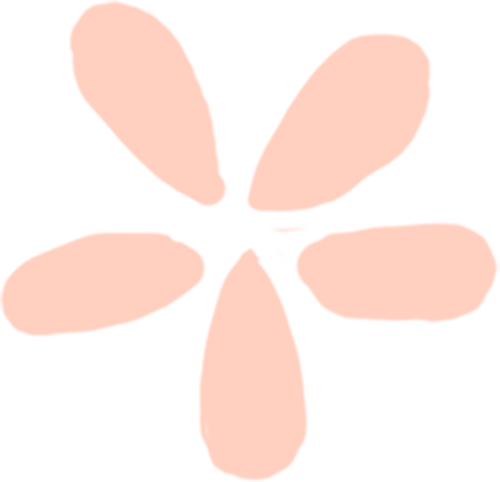
引线键合起源于20世纪60年代初, 被广泛应用于芯片与基板间的电气互连和芯片间的信息交互。 与传统互连材料金(Au)相比, 铜(Cu)丝具有价格便宜、电导率和热导率高、机械性能更优等优势 , 有望取代Au广泛应用于引线键合。 然而,自1992年美国国家半导体公司成功将Cu 引线键合应用于低端电子产品至今, 由于对Cu引线键合机理和可靠性研究的不充分, 工业界仍对大规模应用Cu丝互连采取保留态度 , 因而对Cu引线键合的研究变得迫切。
在芯片封装流程中, 引线键合后需要进行环氧树脂塑封, 这种后成型封装通常需要在175—200◦C温度下退火4—8h。 Cu/Al引线键合界面在键合和退火过程中由于原子扩散会形成金属间化合物。根据Cu/Al二相图在365 ◦C下Cu/Al IMC共有5个稳定相: CuAl2(θ), CuAl(η2),Cu4Al3(ζ2),Cu3Al2(δ),Cu9Al4(γ1)。 近年来, 大量工作集中研究了Cu/Al键合界面IMC和空洞生成,过量的Cu/Al IMC 和空洞不但会增加接触电阻还会降低键合强度。 早期的研究主要基于光学显微镜、 Micro-XRD或者SEM-EDX, 认为键合后(asbonded)键合界面没有Cu/Al IMC生成, 并得到退火后IMC主要有CuAl2, CuAl和Cu9Al4,基于Micro-XRD分析认为150—300 ◦C下Cu/Al IMC的主要成分为Cu9Al4, 并基于SEM研究得到Cu/Al IMC生长速度是Au/Al IMC 生长速度的10%, 给出了IMC生长公式。 随着电子显微镜发展, 一些工作开始利用高分辨扫描电子显微镜(SEM)和聚焦离子束系统(FIB)对Cu/Al IMC在退火处理下从键合后的几纳米生长至几微米的成分演变进行了研究。近年来, 越来越多的研究开始采用高分辨透射电子显微(TEM)技术, 这些工作直观、精确地获得了一些Cu/Al IMC晶格结构的信息,认为175 ◦C, 200 ◦C和250 ◦C退火条件下Cu-Al IMC由CuAl2 转化为Cu9Al4。 然而,目前关于Cu/Al IMC生长的机理依然不够明确,需要进一步深入研究。同时, 综上所述的所有研究方法均采用非原位研究, 即对一批样品进行不同退火温度和退火时间处理, 然后再进行SEM和TEM表征。与非原位实验研究相比, 原位透射电子显微术(In-situ TEM)基于透射电子显微镜, 结合多功能样品杆(对样品进行多外场负载、力电热性能测试等), 可以对材料实现原位处理和同步观测。因而, 原位透射电子显微技术是研究Cu/Al引线键合界面在多种处理环境中结构演化过程和机理的先进方法。
基于In-situ TEM研究了Cu/Al引线键合界面在50—220 ◦C退火下Cu/Al IMC 的结构演变。 通过原位加热观测, 我们分析了Cu/Al IMC的结构演变, 并计算得到了Cu/Al IMC反应速率, 推导得到了原位加热下Cu/Al IMC生长公式。
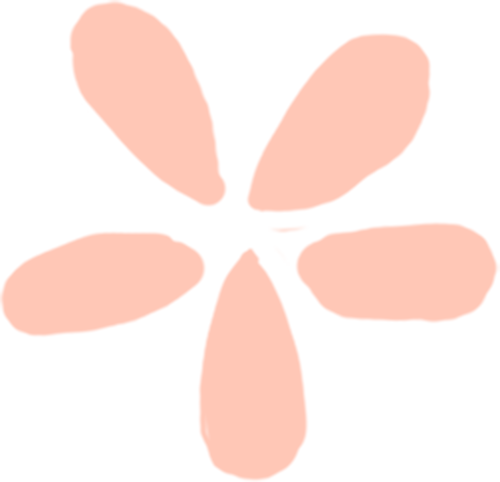
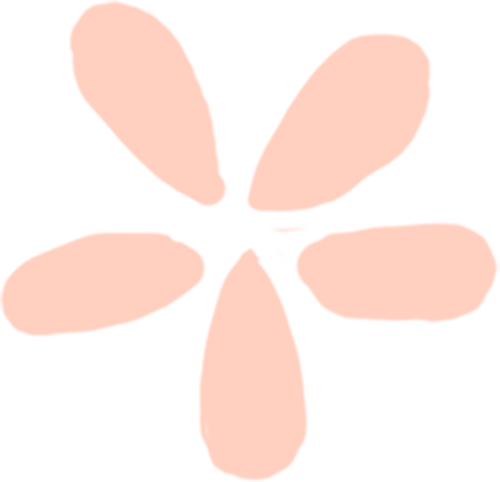
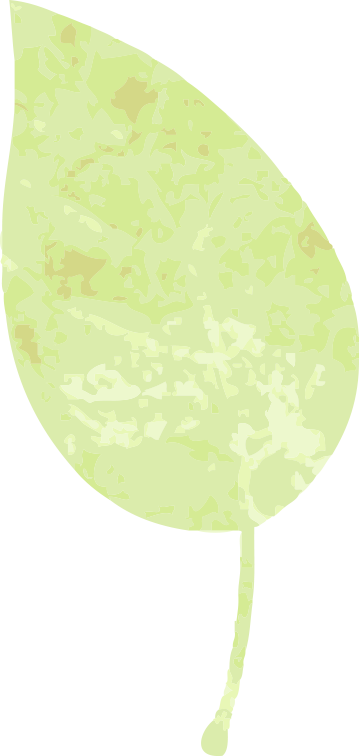
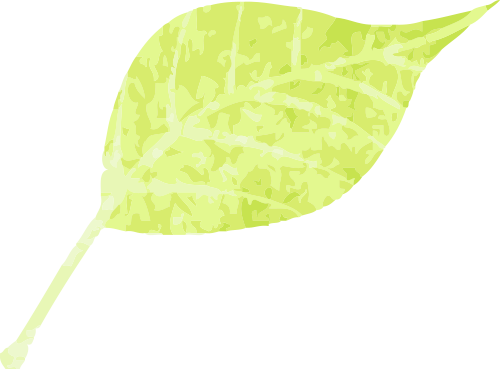
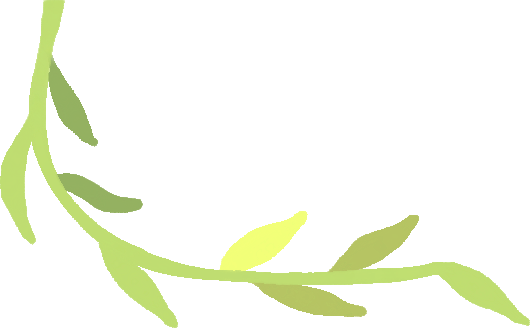
二、实 验
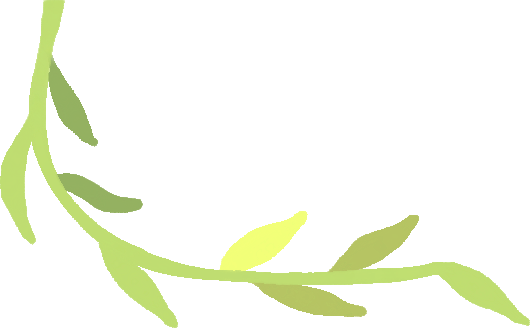
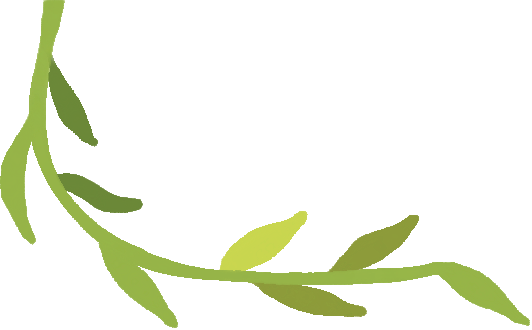
如图 1 (a)所示, 直径为22 µm的纯Cu线热超声键合到1.5 µm厚的Al 金属盘, 键合压力为25—35 gf, 超声功率为120—150 mW, 键合温度为180 ◦C, 键合后进行塑封。 沿键合球中心使用传统研磨和抛光, 然后采用聚焦离子双束(FIB dualbeam)减薄, 制备厚度小于100 nm的TEM样品。图 1 (b)所示的是FIB制样所得TEM样品的结构图, 而图 1 (c)是在退火前样品的Cu/Al引线键合界面颗粒状IMC的形貌。
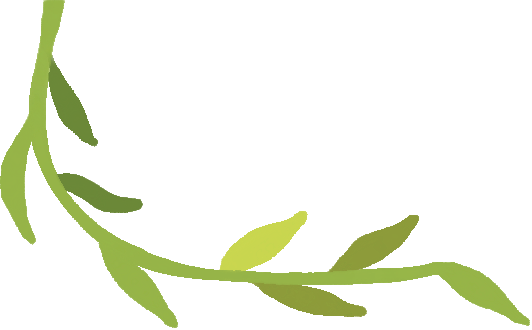
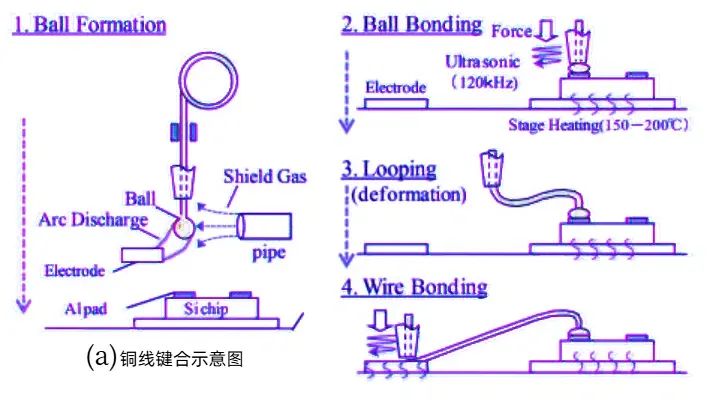
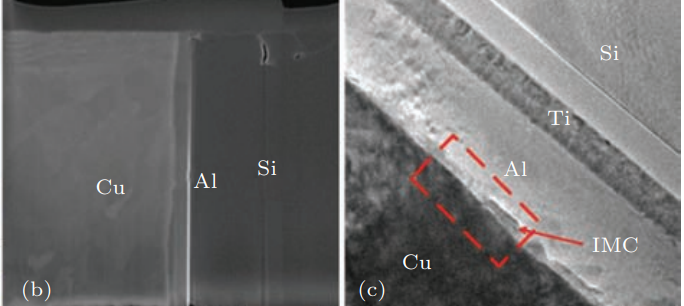
图 1 (a) Cu/Al 引线键合结构示意图; (b) FIB 制样所得原位 TEM 样品结构图 (标尺 = 2 µm); (c) Cu/Al 引线键合界面退火前颗粒状 IMC 形貌 TEM 图 (标尺 = 100 nm)
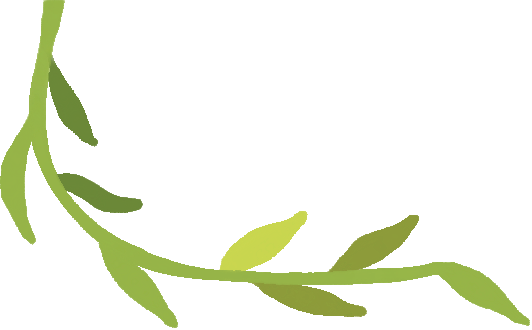
采用加速电压为300 kV带球差校正的透射电子显微镜(FEI Titan 80-300)对FIB样品进行原位表征。 采用Gatan 628单倾热杆进行原位加热, 加热温度从50—220 ◦C逐渐升高, 每个温度下恒温时间超过1 h, 总共持续24 h, 具体加热过程见表 1 。
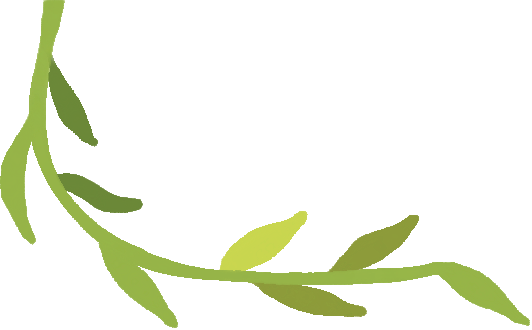
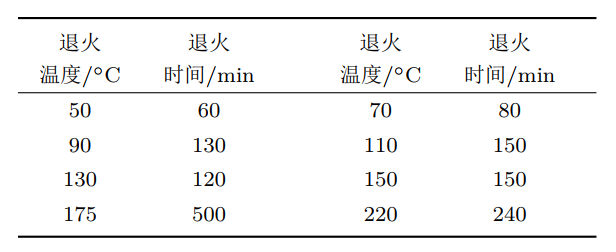
表 1 Cu-Al 引线键合 TEM 样品的原位退火温度和时间
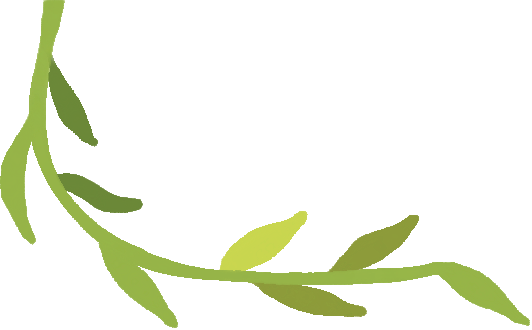
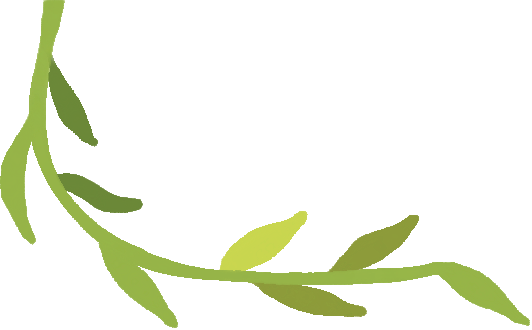
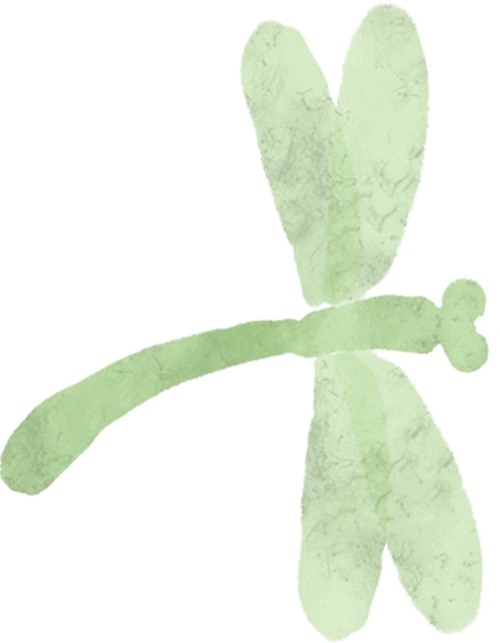
三、结果与讨论
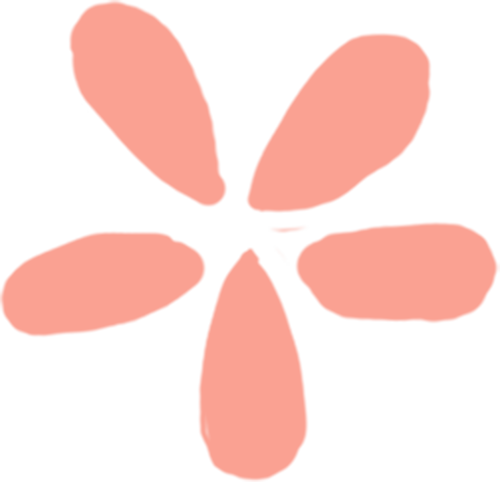
1
Cu/Al IMC生长原位观测

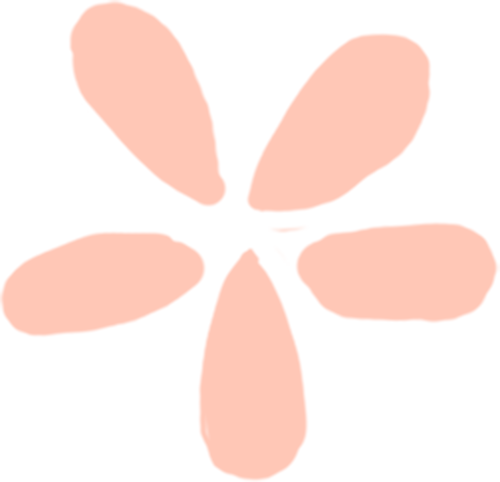
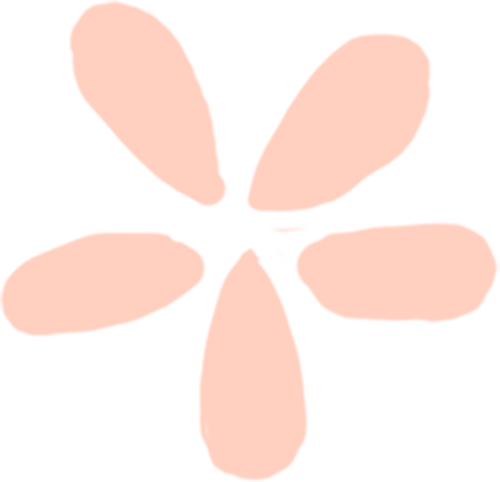
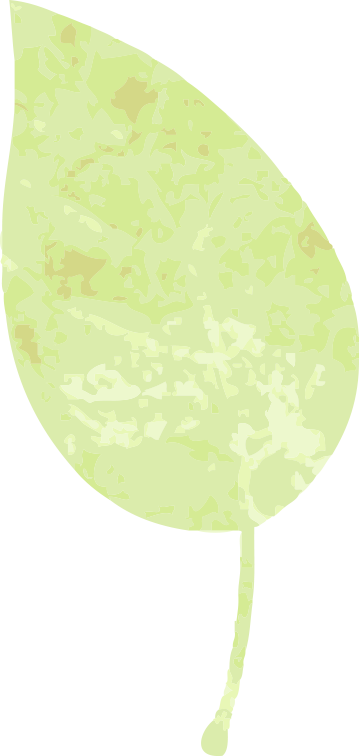
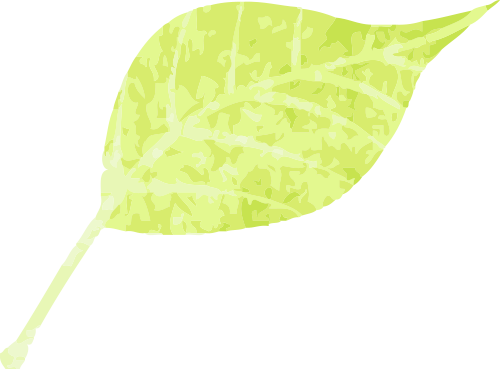
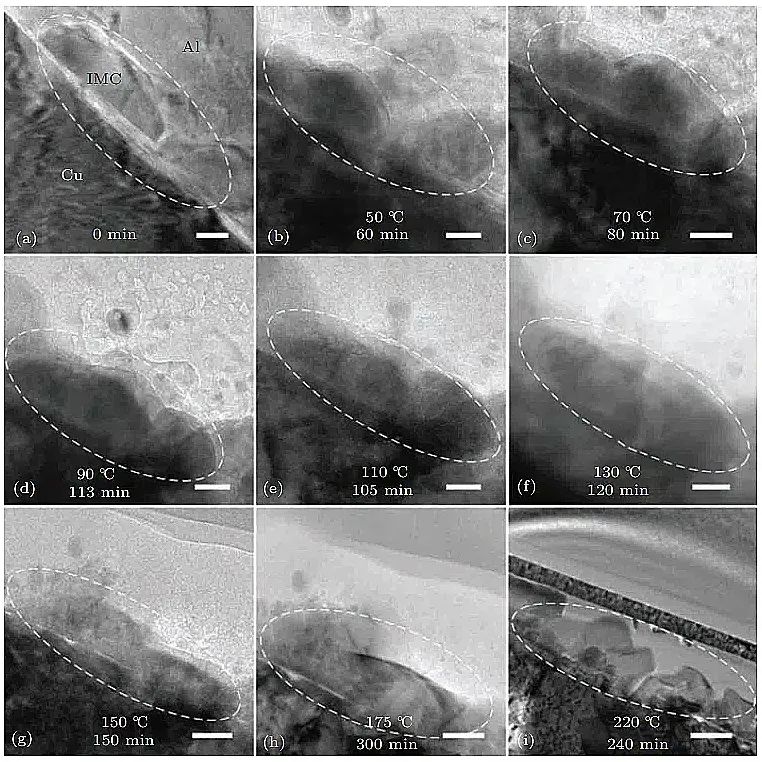
图 2 原位实时观察 Cu/Al 引线键合界面 Cu/Al IMC 热生长动态过程 (a)—(i) 分别为所标注的退火温度和退火时间下的 TEM 图 ((a)—(f) 中标尺 = 20 nm; (g)—(h) 中标尺 = 50 nm; (i) 中标尺 = 0:2 µm)
图 2 为原位加热实时观察到的Cu/Al IMC的动态生长过程图, 图 2 (a)—(i)中白色虚线椭圆中的部分即是Cu/Al IMC。状Cu/Al IMC从初始20—40 nm逐步生长至340 nm, 直至Al几乎全部消耗掉。当退火温度稳定后, 没有观测到Cu/AlIMC的生长速度激增的现象, 所以退火温度稳定后大于一个小时的观测数据足够反映Cu/Al IMC在该温度下的生长情况。 原位观察实验表明, 当温度低于175 ◦C时, IMC生长速度相对缓慢; 当温度高于175 ◦C时, IMC生长速度较快。
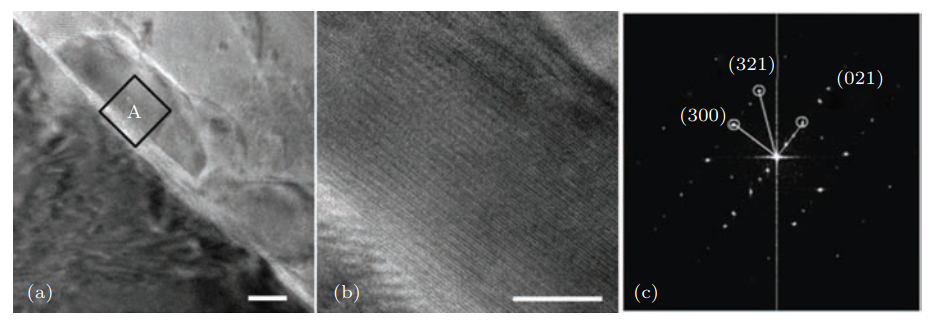
图 3 (a) Cu/Al 引线键合界面退火前颗粒状 IMC 形貌的 TEM 图 (标尺 = 20 nm); (b) 为 (a) 所示区域 A 中IMC 的 HRTEM 像 (标尺 = 10 nm); (c) 为 (b) 所示 IMC 的 FFT 图, 经标定得出为 Cu9Al4
图 3 所示的是退火前Cu/Al引线键合界面的IMC相分析。 退火前IMC呈孤岛颗粒状分布在Cu/Al键合界面, 如图 3 (a)所示。 图 3 (b), (c)分别是(a)所示IMC的高分辨二维晶格像和快速傅里叶转换图(FFT), 此处IMC经过分析确认为Cu9Al4。 分析得到, IMC退火前的主要成分是Cu9Al4, 少量成分是CuAl2。而在其他文献研究中, 退火前IMC的主要成分是CuAl2, 这可能是因为本样品键合之后经过了塑封处理, 塑封过程需要经历一百多摄氏度下数小时热处理。 图 4 (a)为 Cu/Al 引 线 键 合 界 面 经 过 24 h 退 火 处 理 后STEM 形 貌 图, 经 过 分 析 得 到 IMC 主 要 有 两层, 与Cu相近一端为Cu9Al4(图 4 (c)), 另一层为CuAl2(图 4 (b))。然而, 365 ◦C 下Cu/Al IMC的其他稳定相如CuAl, Cu4Al3, Cu3Al2, 在原位加热没有观测到。 其原因可能是这些成分的热稳定性没有CuAl2 和Cu9Al4 高, 也有可能这些结构分布散乱零碎, 不足以进行高分辨表征。
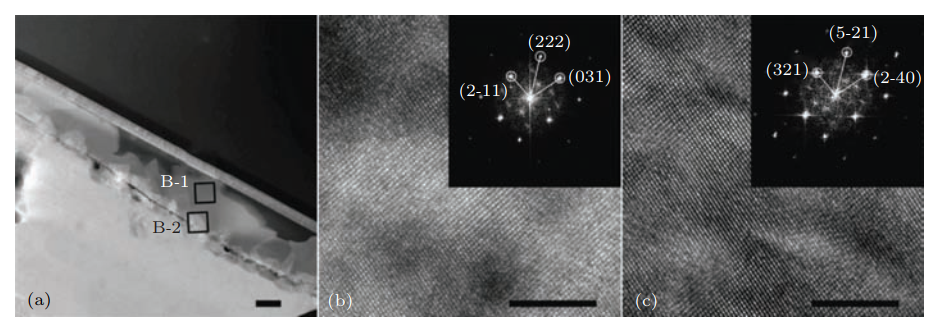
图 4 (a) Cu/Al 引线键合界面根据表 1 退火 24 h 后 STEM 图 (标尺 = 0:2 µm); (b) 为 (a) 所示区域 B-1 中 IMC的 HRTEM 像 (标尺 = 5 nm), 插图为 B-1 的 FFT 图, 经标定得出为 CuAl2; (c) 为 (a) 所示区域 B-2 中 IMC 的HRTEM 像 (标尺 = 5 nm), 插图为 B-2 的 FFT 图, 经标定得出为 Cu9Al4
2
Cu/Al IMC原位生长速率计算

基于非原位加热、SEM表征Cu/Al IMC厚度随温度和时间变化的数据, 给出了Cu/Al IMC生长公式:
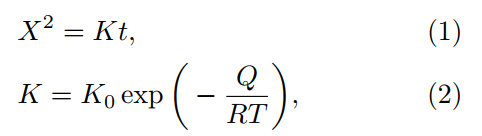
其中X 为IMC厚度(cm), t为退火时间(s), K 为IMC反应速率(cm2/s), K0 为指前因子(cm2/s), Q是激活能(kcal/mol) (1 cal = 4:184 J), R是气体常数(kcal mol−1K−1), T 是退火温度(K), (2)式为阿伦尼乌斯公式,通过计算得到Cu/Al IMC生长公式为

根据(1)式, 本文使用Mathematic软件对原位观测得到的Cu/Al IMC厚度随时间的变化关系数据进行拟合处理, 得到如图5 (a)所示的曲线, 在150 ◦C,175 ◦C, 220 ◦C下Cu/Al IMC厚度随时间近似呈抛物线关系。 利用(1)式进一步对IMC厚度与退火时间的平方根的变化关系数据进行拟合, 可以得到如图 5 (b)所示的拟合直线。 由此, 可以认为原位退火条件下Cu/Al IMC厚度的平方近似正比于退火时间。
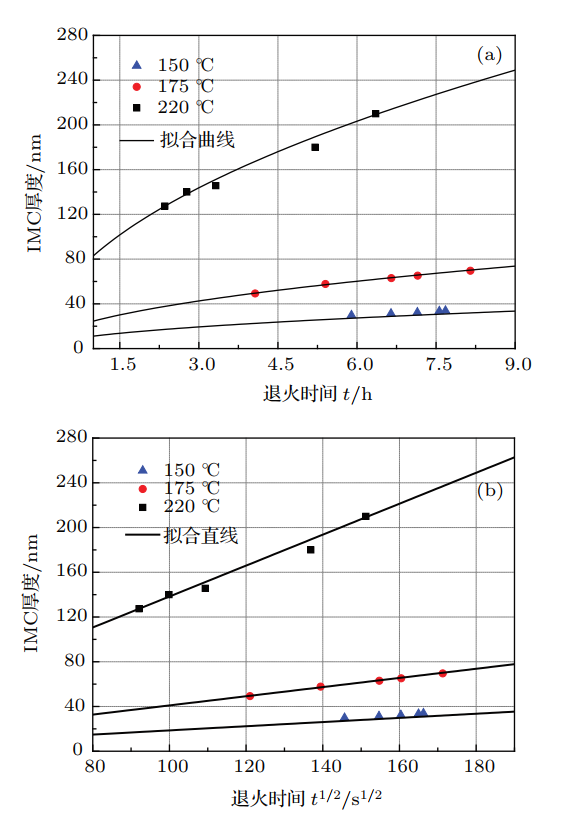
图 5 (a) Cu/Al IMC 厚度与退火时间的关系; (b) Cu/AlIMC 厚度对退火时间的平方根的关系
对于图 5 (b)中的拟合直线, 其斜率即是K1/2的值, 可以得到三种不同温度下K1/2 的值, 从而可以得到不同退火温度下IMC的反应速率如表 2 所示。 同时, 表 2 中也给出了非原位实验研究所得Cu/Al IMC反应速率数据与原位实验研究所得Cu/Al IMC反应速率数据的比较。 从表 2 中可以看到, 本文原位研究所得的反应速率略高于非原位研究得到的反应速率, 且随加热温度升高, 两者的相对相差(绝对相差/平均值)逐渐减小。 由表 2 中的数据, 根据(2)式对Cu/Al IMC反应速率的自然对数随退火温度的倒数的变化关系数据进行拟合, 得到如图 6 所示的拟合直线。 根据图 6 中拟合直线的斜率和截距可以得到了原位实验研究Cu/Al IMC生长公式为

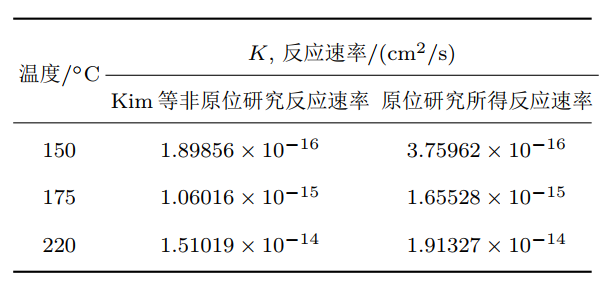
表 2 原位和非原位研究方法得到的 Cu/Al IMC 反应速率的比较
比较可知, (3)式和(4)式形式一致, 但是系数不同。为了进一步比较两种方法所得公式的差异, 根据(2)式计算了Cu/Al IMC的激活能Q。如表 3 所示, 原位实验研究所得Cu/Al IMC激活能为23.8 kcal/mol, 而基于SEM非原位实验研究计算得到的Cu/Al IMC 激活能为26 kcal/mol。

表 3 不同研究方法得到的 Cu/Al IMC 激活能比较
基于TEM非原位实验研究分别计算得到CuAl2 和Cu9Al4 的激活能为14.49kcal/mol, 18.06 kcal/mol。从表 3 中比较可知, 原位透射电子显微镜研究所得Cu/Al IMC 的激活能介于SEM和TEM非原位实验研究中间。 如上所述, 由于键合工艺的偏差和Cu/Al IMC不同部位生长的非均匀性, 采用非原位研究方法, 需要在一批样品热处理后再分别进行制样观测。 由于样品本身的差异, 这种非原位的方法相比于原位实验研究将产生较大的误差。 同时, 非原位实验研究中, 一组样品之间退火时长的间隔从几小时到几十小时不等, 长时间的缺乏监控, 将大大增加生长过程中的不确定性。 而原位透射电子显微镜研究, 不但提供了实时观测Cu/Al IMC热生长的可能, 还可以更加精确地测量Cu/Al IMC生长。 精确的Cu/Al IMC生长公式, 对准确地预测Cu/Al引线键合的可靠性具有重大意义, 对Cu/Al引线键合产品的正确使用环境提供了指导, 甚至对芯片设计中散热标准提出了指导。
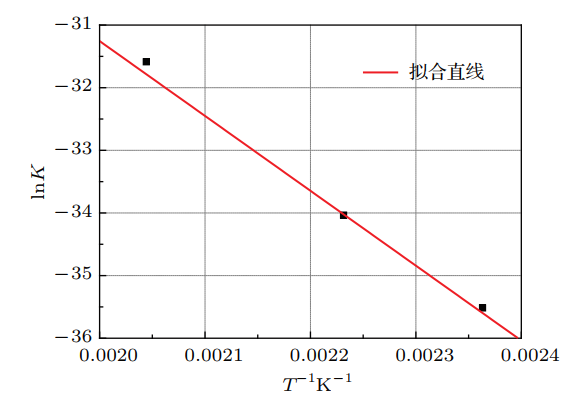
图 6 Cu/Al IMC 反应速率的自然对数 lnK 与退火温度T 的倒数关系
四、结论
本文基于原位高分辨透射电子显微镜实时观测了Cu/Al引线键合界面金属间化合物退火条件下的结构演变过程。 实验表明, 退火后CuAl IMC的主要产物为CuAl2 和Cu9Al4。 同时, 拟合计算得到了不同退火温度下Cu/Al金属间化合物的反应速率和激活能(23.8 kcal/mol), 给出了基于原位实验结果的更加精确的Cu/Al IMC生长公式, 为Cu/Al引线键合的应用、芯片散热设计和可靠性预测提供了指导。