隔离方法
集成电路 (IC) 实现隔离的方式是阻断直流和低频交流电流,而允许电源、模拟信号或高速数字信号通过隔离栅传输。图1展示了三种用于实现隔离的常用半导体技术:光学(光耦合器)、电场信号传输(电容式)和磁场耦合(变压器)。
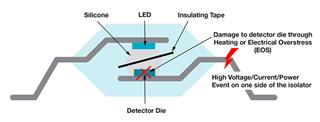
(a)
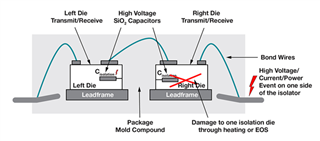
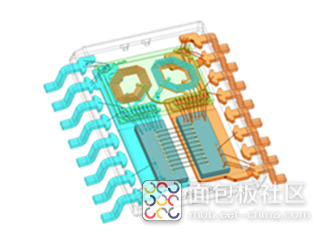
(c)
图 1:半导体隔离技术:光耦合器 (a);电容式 (b);变压器 (c)
利用可靠隔离技术克服高电压设计挑战
电容隔离
电容隔离技术基于穿过电介质的交流信号传输。TI 的电容隔离器使用介电强度很高的 SiO2 电介质构建。因为SiO2为无机材料,所以在不同湿度和温度条件下都非常稳定。 此外,我们专有的多层电容器和多层钝化方法可降低高电压性能对任何单层的依赖,从而提高隔离器的质量和可靠性。我们的电容技术支持的工作电压 (VIOWM) 为2kVRMS,可承受的隔离电压 (VISO) 为7.5kVRMS,并且能够承受12.8kVPK的浪涌电压。
磁隔离
磁隔离通常用于需要高频直流/直流电源转换的应用。IC变压器耦合隔离的一个优势是可以传输超过数百毫瓦的功率,通常无需次级侧偏置电源。也可以使用磁隔离来发送高频信号。在需要同时输送电力和传输数据的系统中,您可以使用相同的变压器绕组线圈来满足功率和信号需求,如图2所示。将信号和电力输送功能结合到同一集成变压器线圈上,可以充分降低解决方案的成本并缩小尺寸。
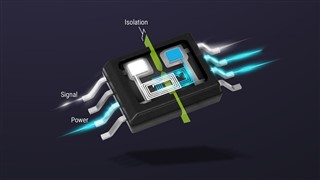
图2:使用磁隔离通过隔离栅可靠地输送电力和信号
对于磁隔离,TI使用专有多芯片模块方法,协同封装高性能平面变压器与隔离式功率级和专用控制器裸片。我们可以使用高性能铁氧体磁芯来构建这些变压器,以便提高耦合和变压器效率,也可以在电力输送需求不高的应用中使用空芯,从而节省成本并降低复杂性。 可靠地满足隔离需求,同时缩小解决方案尺寸并降低成本。
不同应用所需的隔离方法不尽相同。
电动汽车应用
为减轻重量、增加扭矩、提高效率并加快充电速度,电动汽车高电压电池组的电平从 400V增加到800V,甚至高达1kV。电池管理系统 (BMS) 和牵引逆变器是两个非常关键的电动汽车子系统,需要将800V域与底盘隔离,从而确保乘客及其车辆的安全。
图3所示框图是牵引逆变器的示例,在三相直流转交流逆变器配置中,该牵引逆变器使用隔离栅极驱动器来驱动高电压绝缘栅双极晶体管 (IGBT) 或碳化硅 (SiC) 模块。这些模块可协同封装多达六个IGBT或SiC开关,至多需要六个隔离变压器,为六个独立的栅极驱动器IC供电。我们的 UCC14240-Q1是一款双输出、中电压、隔离直流/直流电源模块,可在牵引逆变器、栅极驱动器偏置应用中实现更高的性能,同时通过减少外部变压器的数量来充分缩小PCB面积。
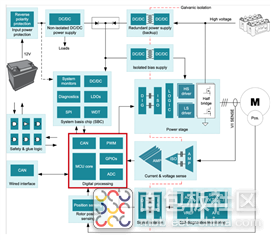
图 3:典型的牵引逆变器系统方框图
此外,将高电压电池端子连接到子系统时,BMS使用预充电电路。我们的5kVRMS TPSI3050-Q1隔离开关驱动器旨在取代机械预充电接触器,实现更小、更可靠的固态解决方案。该器件可提供高达5kVRMS 的增强型隔离,工作寿命为机电继电器的10倍,且不像机电继电器那样容易随着时间的推移而退化。图4说明了 TPSI3050-Q1与机械继电器相比所能节省的面积。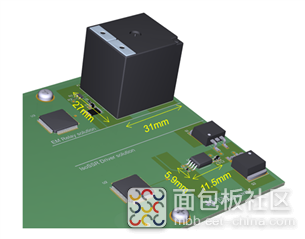
图 4:使用基于磁隔离的固态继电器驱动器 (TPSI3050) 缩小解决方案尺寸
电网基础设施应用隔离是电网基础设施应用中的必备要素,它能够保护设备和人员免受高压浪涌的损害,消除互连时涉及较大接地电位差 (GPD) 的破坏性接地回路,并在共模瞬态事件期间保持数据完整性。
太阳能设备和电动汽车充电器的工作电压范围为200V至1,500V或更高。图4所示为我们高压电动汽车充电和太阳能中的绝缘监测AFE参考设计。该参考设计使用我们的 AMC3330精密隔离放大器和 TPSI2140-Q1隔离开关,在电网基础设施应用中监测绝缘电阻。由于没有移动器件,这种固态继电器解决方案可以执行数十年的频繁测量,且不会降低性能。电力和信号均可通过TPSI2140-Q1内的隔离栅输送,因此无需次级侧偏置电源。由于该器件采用薄型小尺寸IC (SOIC)封装,因此解决方案尺寸可以比基于光继电器或机械继电器的解决方案小50%。
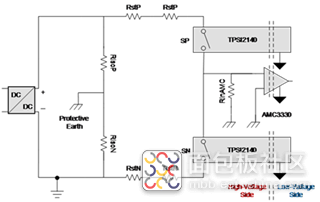
图5:高压电动汽车充电和太阳能中的绝缘监测AFE方框图
来源:TI