(报告出品方/作者:东北证券,李恒光、韦松岭)
1. 精密减速器——机器人成本占比最高的核心零部件1.1. 减速器分类及精密减速器简介
减速器可分为通用减速器、精密减速器和专用减速器。减速器作用是把高速运转的 动力,通过输入轴上齿数少的齿轮啮合输出轴上齿数多的大齿轮,从而达到改变输 出转速、扭矩和承载能力的目的。减速器按用途可分为三大类:①通用减速器(一 般传动减速器)控制精度较低,可满足机械设备基本的动力传动需求;②专用减速 器主要应用于汽车、工程机械、航空航天等特定行业;③精密减速器背向间隙小、 精度高、更加可靠稳定,更加适用于机器人、数控机床等高端领域。
精密减速器是工业机器人的三大核心零部件之一,成本占比超 30%。工业机器人被 誉为“制造业皇冠顶端的明珠”,其研发、制造、应用是衡量一个国家科技创新和高 端制造业水平的重要标志。而精密减速器又是工业机器人的三大核心零部件之一, 通常精密减速器占工业机器人成本的 30%以上,成本占比最高、研发难度最大。
精密减速器种类较多、型号各异。全球机器人领域使用的精密减速器包括 RV 减速 器、谐波减速器、精密行星减速器、摆线针轮减速器、滤波减速器等。其中 RV、谐 波减速器的市场销售数量占比大约分别为 40%、40%。
1.2. 各类精密减速器传动原理及结构特点
1.2.1. 精密行星减速器:成本低、传动效率高、承载能力强,但重量体积大、单级 减速比小
精密行星减速器主要由太阳轮、行星轮、内齿圈构成,其减速传动原理就是齿轮减 速原理。通过太阳轮输入转速与行星轮啮合,行星轮啮合自转的同时围绕中心轮公 转,最后由行星架将转速和扭矩传到输出轴上。精密行星减速器通过对重量结构精 密化,以及严格的零部件制造和装配工艺控制,获得相对普通行星减速器具备更为 优异的性能,通常配合步进电机或伺服电机应用于工业机器人关节中。
精密行星减速器优势: (1) 相对普通行星减速器体积重量小,精度高。通过对重量结构精密化,以及严 格的零部件制造和装配工艺控制,获得相对普通行星减速器更优异的性能指 标。 (2) 传动效率高。行星减速器传动结构对称,均匀分布的行星轮使得作用中心轮 与行星架轴承的反作用力相互平衡,能有效提高传动效率,单级传动效率可 达 97-98%。 (3) 承载能力强、抗冲击和振动性能好,运动平稳。多个行星轮的使用增加啮合 齿数、分担载荷,对称结构使得惯力平衡,提高了减速器的承载能力。 (4) 结构简单、成本相对谐波、RV 低。通常行星减速器价格低于 500 元。
精密行星减速器劣势: (1) 单级精密行星减速器传动比小,多级减速的长度重量限制其使用场景。精密 行星减速器单级传动减速比最小为 3,最大一般不超过 10。当一级行星齿轮 传动系统无法满足较大减速比需要时,则需 2-3 级减速来满足较大的减速比 需求。但由于增加了传动级数和齿轮数量,多级精密行星减速器的长度重量 也会有所增加,这限制了其使用场景。 (2) 需要定期维护,同时高精度、高效率等特殊要求会带来更高的制造成本。精 密行星减速器需要定期维护和保养(包括定期更换润滑油和维修传动部件 等),以确保其长期可靠性。同时对于精度、效率等的额外要求会相应增加 制造成本,例如人形机器人若要使用行星减速器则需要对电机进行扁平化设 计,同时行星减速器也需要定制成微型多级传动的形式(但不排除部分特定 场合使用定制化行星减速器仍具备经济效益)。
1.2.2. RV 减速器:体积质量较小、减速比范围大、承载能力强,但工艺复杂、成 本高
RV 减速器由摆线针轮行星传动发展而来。RV 减速器是 20 世纪 80 年代日本帝人精 机(2003 年与纳博克合并成立纳博特斯克)在传统摆线针轮减速器和行星减速器的 基础上研发的一种 2 级减速机构,结构上可以看成是由第 1 级的行星齿轮减速部分 和第 2 级的摆线针轮减速部分组合而成。其秉承了传统行星和摆线针轮减速器高刚 性、高精度等特点,同时克服了体积重量大、传动比低的问题,在工业机器人、数 控机床、医疗检测设备、卫星接收系统等领域广泛使用。
RV 减速器的传动原理: 一级减速装置为行星齿轮结构,由输入齿轮(太阳轮)和行星轮组成。 (1) 输入齿轮与电机相连同步旋转,带动 2-3 个行星轮同时转动。由于行星轮的 齿数较多、形状较大,因此行星轮的转动速度慢于输入齿轮,实现第一级减 速。 (2) 曲柄轴前后端分别与行星轮和摆线轮相连,在行星轮旋转后,曲柄轴以相同 的转速旋转。
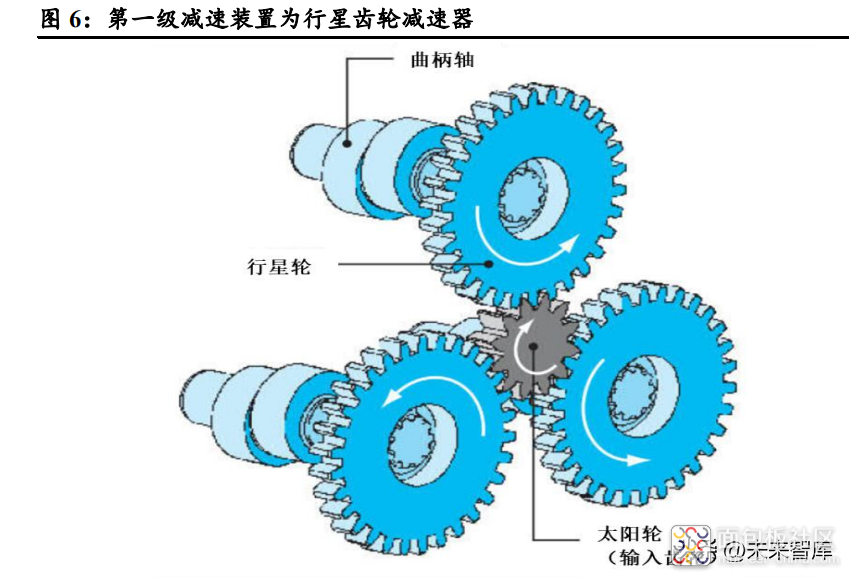
第二级减速装置为摆线针轮传动,主要由滚动轴承、摆线轮、针轮等结构组成。 (3) 曲柄轴上含有偏心部,偏心部与滚动轴承相连接,摆线轮在滚动轴承的作用 下随曲柄轴运动。RV 减速器通常有 2 个摆线轮,2 个摆线轮相位差为 180 度,用于抵消运动过程中的径向跳动,提升精度的同时,提高安全系数和抗 冲击强度。(4) 在外壳内侧有与摆线轮同等齿距排列的针齿,其数量比摆线轮齿数多一个。 曲柄轴旋转一圈,摆线轮与针齿接触的同时做一圈偏心运动。在针轮保持固 定的情况下,摆线轮沿着与曲柄轴的旋转方向相反的方向旋转一个齿数的距 离,实现第二级减速。 (5) 摆线轮外接输出轴,并向外实现最终传动。最终减速比为一二级减速比的乘 积。
RV 减速器具有结构紧凑、体积小质量轻、减速比大、承载能力强、寿命长、精度 稳定等一系列优点。 (1) 结构紧凑,体积小质量轻。行星传动结构与紧凑的 W 输出机构组合,使整 个摆线针轮减速装置结构十分紧凑,因此其结构体积小、质量轻。 (2) 减速比范围大,传动效率高。RV 减速器为两级传动,摆线针轮传动的减速 比大小取决于摆线针轮的齿数,齿数越多减速比越大,因此减速比较传统行 星减速器和摆线针轮减速器更高,同时传动效率可达 85%~92%。 (3) 承载能力强,传动平稳。摆线轮呈 180°相位角对称分布,使得摆线轮受力 均匀;同时啮合齿数较多,增加了减速器的传动平稳性和承载能力。另外, 采用两端支撑的输出结构,比普通的摆线减速器具有更大的刚性、更高的抗 过载冲击性能。 (4) 在正确的设计和严格的制造工艺保证下,可获得较高的传动精度。
RV 减速器的劣势: (1) 结构复杂,制造工艺和成本控制难度大。 (2) 产线投资相对其他类型精密减速器更高。 (3) 体积重量相对谐波减速器大。
1.2.3. 谐波减速器:体积质量小、减速比范围较大,但承载能力较弱、容易疲劳损 坏
谐波减速器的三个基本构件:波发生器、带有外齿圈的柔性齿轮(柔轮)、带有内齿 圈的刚性齿轮(刚轮)。三个构件可任意固定一个,其余两个一为主动、一为从动, 可实现减速或增速(固定减速比),也可变换成两个输入,一个输出,组成差动传动。
谐波传动的原理是利用柔轮可控的弹性形变来传递运动和动力。最常见的谐波传动 模式及原理是波发生器主动、刚轮固定、柔轮输出的形式。将波发生器装入柔轮内 圆中,迫使柔轮在凸轮作用下产生变形而呈椭圆状,使其长轴处柔轮齿轮插入刚轮 的轮齿槽内,成为完全啮合状态;而其短轴处两轮轮齿完全不接触,处于脱开状态, 当波发生器连续转动时,迫使柔轮不断产生变形并产生了错齿运动,从而实现波发 生器与柔轮的运动传递。
谐波传动具有传动精度高、减速比大、体积小重量轻、传动平稳、可向密封空间传 递运动等优点。 (1) 传动精度高。多齿在两个 180 度对称位置同时啮合,因此齿轮齿距误差和累 积齿距误差对旋转精度的影响较为平均,可得到极高的位置精度和旋转精度。 (2) 减速比大。单级谐波齿轮传动的减速比可达 30~500,且结构简单,3 个在同 轴上的基本零部件就可以实现高减速比。(3) 体积小、重量轻。谐波减速器结构简单零件少,与一般减速器比较,在输出 力矩相同的情况下,体积可减少 2/3,重量可减轻 1/2。 (4) 传动平稳。由于同时啮合的齿数多,齿面相对滑动速度低,使得谐波减速器 承载力高,传动平稳。 (5) 能在密闭空间和介质辐射的工况下正常工作。这是其他类型减速器不具备 的特征,广泛应用于军工、航空航天、船舶潜艇、宇宙飞船等领域。
谐波减速器的劣势: (1) 柔轮易发生疲劳破坏,刚性差,承载能力有限。谐波减速器是通过柔轮不断 发生变形来传递扭矩的,极易引起材料的疲劳损坏,同时随着使用时间增长 运动精度可能会显著降低。这决定了其承受大扭矩和冲击载荷的能力有限, 因此一般运用在轻负载部分。 (2) 成本相对精密行星减速器高,但低于 RV 减速器。 (3) 转动惯量和启动转矩大,不适合小功率跟踪传动。 (4) 散热条件差。
2. 特斯拉人形机器人持续进化,精密减速器不可或缺2.1. 机器人减速器选型关注多项核心指标,RV 和谐波减速器是当前主流
在进行机器人零部件选型时,需要根据机器人应用场景以及结构设计等因素选择输 出电机和减速器,通常减速器关注尺寸大小、传动精度、减速比、扭矩等核心指标。 (1) 背向间隙是衡量减速器精度等级的主要参数。减速器内部各零件之间均存 在间隙,当减速器输入轴转向改变时,输出轴滞后一定的角度才会响应。减 速器输出轴上的滞后角被定义为减速器的背隙,背隙是减速器产生振动、噪 声,和影响减速器寿命、工作精度及可靠性的重要参数。 背隙大小会对传动效率产生影响,同时会产生振动和噪音。如果背隙太大, 输出轴的运动就会出现明显的滞后,会导致传动效率降低,同时也会增加设 备的运行噪声和振动。而如果背隙太小,又会导致行星齿轮与内齿圈之间的 摩擦增加,从而使传动效率降低并缩短设备寿命。
(2) 传动效率:传动效率是指输出功率与输入功率的比值。传动效率受到背隙、 减速比、转速、负载扭矩、温度、润滑等因素影响。通常行星减速器传动效 率>RV 减速器>谐波减速器。 (3) 减速比:指减速机构中瞬时输入速度与输出速度的比值。通常用于衡量减速 器的减速性能,其数值越大,表示输出轴角速度越小,即减速效果越明显。 行星减速器由于结构原因,单级减速最小为 3,最大一般不超过 10,大减速 比行星减速器需要通过多级传动实现。RV 和谐波减速器减速比范围则远超 一级行星减速器。 (4) 额定输出转矩:指减速器长时间(连续工作制)可以加载的扭矩。减速比与 扭矩正相关,减速比越大扭矩越大,但转速越小。 (5) 扭转刚性:衡量减速器构件在扭转力矩作用下的抗变形能力。RV 减速器的 扭转刚性明显优于谐波减速器。
RV 和谐波减速器是目前机器人领域主流的两种精密减速器,高减速比行星减速器 因体积较大不适用于对零部件尺寸要求较高的部分机器人。RV 和谐波减速器的特 点是厚度薄、体积小、重量轻,同时具备较大的输出力矩(单位体积输出力矩大), 而刚性和连续运转时间则不如行星减速器。但与 RV、谐波减速器相比,相同或更高 减速比的行星减速器通常为三级或以上,因此高减速比的行星减速器一般长度较长、 体积较大,不适用于对零部件尺寸有较高要求的部分机器人。 RV 和谐波减速器在精度、扭矩、刚度、传送效率等性能指标上各有不同。RV 减速 器一般由行星齿轮减速器的前级和摆线针轮减速器的后级组成,因此具备行星减速 器和摆线针轮减速器的部分特征。相比谐波减速器,RV 减速器具有更高的刚性和扭 矩承载能力,但重量更重、外形尺寸更大。同时 RV 减速器零部件数量也较谐波减 速器更多、制造和装配难度大,不利于大规模生产,价格也较谐波减速器偏贵。
在输出力矩相同时,谐波减速器较一般减速器体积小 2/3,重量轻 1/2,但谐波减速 器负载轻,容许力矩负载在 1500Nm 以内。而 RV 减速器减速比范围比谐波减速器 大、精度较为稳定、疲劳强度较高,并具有更高的刚性和扭矩承载能力,容许力矩 负载可达 8000Nm。 RV、谐波减速器适用领域互补,不能完全相互取代。谐波减速器的负载范围限制了 其向重负载部位拓展的可能,而 RV 减速器重量、体积相对较大的特点也使其无法 向轻便、灵活的轻负载领域发展,两者适用领域不同并不能完全相互取代。通常多 关节机器人中负载较重的机座、大臂、肩部等位置使用 RV 减速器,协作机器人、 服务机器人、以及人形机器人小臂、腕部、手部等轻负载领域则是谐波减速器占据 主导地位。
2.2. 人形机器人对减速器小型化、轻量化要求高,谐波和 RV 减速器最 适配
特斯拉人形机器人一经推出就引起市场广泛关注。随着我国人口红利消退,劳动供 给减少用工成本上行,“机器换人”也成为了近年的发展新趋势。人形机器人由于接 近人体构造,工作场景适应能力强,被认为是未来替代人类从事的各类危险、重复 或无聊工作的最可能选择,发展前景广阔。 人形机器人能够与人类协同作业并完成各种生产制造任务,尤其在机械装配、高速 作业、货物分拣搬运等领域对降低工人劳动负担、提高生产效率和保障作业安全具 有重要作用。但同时,相对传统工业机器人,人形机器人对人机协作安全性要求更 高,因而不断降低体积重量、提高输出能力、改善动态性能是近年来协作型仿人机 器人领域的研究重点。 驱动单元是影响人形机器人性能的核心部件。驱动单元起到输出扭矩、驱动机器人 部件运动的作用,占据了人形机器人的大部分重量。其性能不仅直接影响机器人关 节的输出能力,也决定了机器人系统的动态性能上限。
目前市场上仿人机器人的驱动单元主要有三种类型:传统驱动单元、串联弹性驱动 单元和准直驱驱动单元。 (1) 传统驱动单元:一般采用高转速、低扭矩电机搭配高传动比减速器,输出扭矩 大、运动精度高。但人形机器人小型化、轻量化需求对减速器的体积和重量要 求极高,目前主要使用谐波减速器及少部分 RV 减速器,高减速比精密行星减 速器仍存在一定使用障碍。 (2) 串联弹性驱动单元:其与传统驱动单元的区别在于输出端和负载之间采用弹性 部件连接,优势是弹性部件提高了驱动单元的柔度,使机器人关节柔顺性得到改善。但弹性部件对高频运动的响应性差,导致驱动单元系统带宽低、动态性 能差,无法应对实际工况的复杂快速变化。
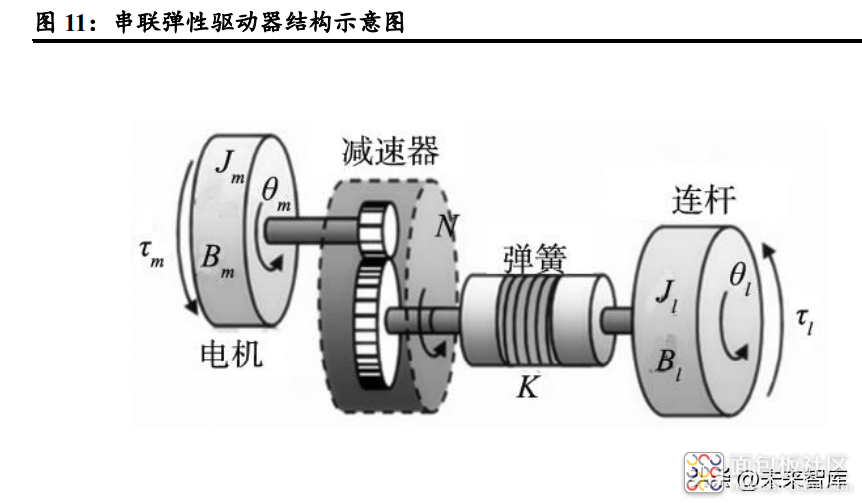
(3) 准直驱驱动单元:大多采用高扭矩密度电机搭配低减速比行星齿轮减速器,驱 动单元在输出较高扭矩的同时还具有重量轻、动态性能好等优势。但高扭矩密 度电机通常体积较大,同时对机器人电源输出功率要求高,运动精度也不可避 免地受到齿轮啮合回差的影响。参考特斯拉人形机器人,其设计电池容量 2.3kWh,电压 52V,全身供 28 个电机关节,同时考虑驱动单元体积重量、输 出功率以及续航问题,高扭矩密度电机+低减速比行星齿轮减速器并不适合作 为主要驱动方案。
特斯拉人形机器人的结构设计及性能定位使得传统驱动方案成为重要的选择之一。 目前特斯拉人形机器人的使用场景仍在不断开发,同时驱动方案也仍在不断改进。 但从设计理念与其“协作型仿人机器人”的产品定位来看,传统“电机+减速器”的 驱动方式仍然是较为契合的技术路线。
自 2021 年特斯拉首次公布人形机器人项目以来,“擎天柱”的进步肉眼可见。在 2023 年 5 月的特斯拉股东大会上,特斯拉人形机器人更是展现了不少精准操作的能力, 产品落地并实现产业化似乎渐行渐近。未来特斯拉人形机器人能否能实现马斯克 “大规模生产、且售价低于 2 万美元”的目标,我们认为技术进步与降本是核心。 那么精密减速器作为传统驱动单元的最核心部件,就要朝轻量化、集成化、产业化 (低成本)的方向发展。