特斯拉机器人全身共使用 40 个关节执行器(又称为关节模组)。关节执行器是 模仿人体的关节而诞生,最早由美国科尔摩根公司发明,供应给协作机器人厂商。 特斯拉机器人关节模组使用的数量和目前全球领先的人形机器人基本一致,可以在 机器人运动过程中实现稳态控制。随着特斯拉机器人在形态越来越接近人类,使用 的关节模组数量或将进一步增长,带动核心部件的市场空间持续增长。
特斯拉机器人在设计上也选择了硬成本最低、软成本最大的方式后发制人。特 斯拉机器人硬件成本包括 40 个关节执行器以及其他结构件,目前硬件成本占 BOM 表比例超过 50%,要达到 2 万美金售价还有 84%的降价空间。 特斯拉机器人关节执行器采用的零部件种类和现有的工业机器人基本一致,由 于没有像工业机器人一样对实现高速运动的要求,一定程度上降低了生产难度,因 此只需根据人形机器人的特点对零部件进行调整修改就可以进行标准化的大批量生 产,而且轴承、齿轮箱、滚珠丝杠、电机等部件可复用特斯拉汽车的供应链。国产 硬件供应商具备很强的低成本大规模量产能力,迎来了导入特斯拉机器人硬件供应 链的重要机遇。
1、旋转关节
旋转执行器包括无框电机、谐波减速器、双编码器、力矩传感器、角接触轴承 交叉滚子轴承。根据我们测算,无框力矩电机、谐波减速器和力矩传感器是旋转关节中价值量占比最高的零部件。从早期阶段推演到终局状态(特斯拉机器人单机售 价 2 万美金时),降价空间最大的为无框电机(降价 75%)、谐波减速器(降价 75%)、角接触轴承(降价 64%)。
1.1、传感器与编码器
特斯拉机器人的旋转关节采用高低速双编码器和力矩传感器。输出侧和电机侧 各有一个编码器。输出侧编码器用于测量输出位置的变化,电机侧编码器用于计算 得到输出轴的理论位置,与输出侧编码器的数据进行对比,得到外部受力大小,从 而交付驱动器进行后续控制。非接触式力矩传感器是基于编码器或霍尔原理测量材 料形变的力矩传感器。
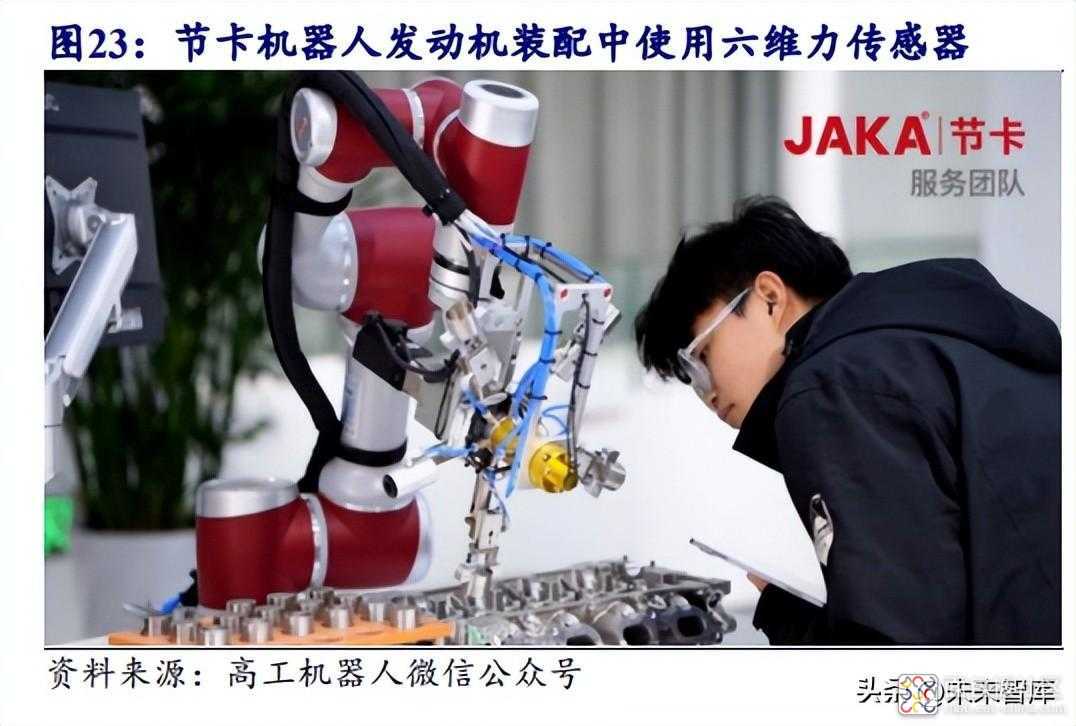
编码器是提供反馈的传感器,机器人编码器是伺服控制的核心部件,伺服控制 性能提高,必然要求编码器精度的提高。从物理介质的不同来分,分为光编码器和 磁编码器。磁编码器成本相较光编码器可以下降 100 多元,但磁编码器的精度低于 光编码器。整体来看,国产编码器的精度和综合性能和国外差距较大,国内高精度 市场被日本厂商多摩川和尼康垄断。国产厂商汇川技术、埃斯顿、昊志机电、奥普 光电(主要用于军工领域)已经实现编码器的自研,但主要面向中低端市场。
力传感器是感知并度量力的关键部件。根据 global information 测算,全球力传 感器市场预计将从 2021 年的 74.3 亿美元增长到 2027 年的 126.6 亿美元。 按照测量维度,力传感器可以分为一至六维力传感器。六维力传感器是目前维 度最高、力觉信息反馈最为全面、难度最大的力觉传感器,最早应用于航空航天市 场,后逐步应用于打磨、铣削、焊接及装配场景的工业机器人以及对传感性能要求 更高的协作机器人。一台进口的六维传感器价格接近国内一台协作机器人的价格, 考虑成本管控,我们认为特斯拉机器人在量产初期基本不会使用六维传感器,使用 一维传感器可能较大。全球传感器市场的主要厂商有霍尼韦尔、意法半导体、飞思卡尔、博世、飞利 浦等,中国市场上的高端传感器进口占比高达 85%,国产化率低。
1.2、谐波减速器
精密减速器是机器人的核心传动部件,占据工业机器人 30%的零部件成本。其 作用是降低伺服电机的高转速、通过齿轮减速比放大伺服电机的原始扭矩,并提供 高刚性保持、高精度定位。谐波减速器是精密减速器的一种,根据《中国工业机器 人发展白皮书》,2021 年全球工业机器人用谐波减速器市场规模为 108.3 亿元。 需求侧:特斯拉机器人的旋转关节需要更轻量、小型、集成化的传动装置,全 身 16 个旋转关节中各使用 1 个谐波减速器。根据我们测算,当特斯拉机器人实现 100 万产量时,谐波减速器新增市场规模达到 73 亿元。
供给侧:日本哈默纳科是全球谐波减速器龙头,占据 70%的份额。总产能基本 稳定在 200 万台/年,并且几乎全部供应给以四大家族为主的工业机器人厂商。哈默 纳科产线的自动化程度较低,对检测人员需求较大。在美德日三地劳动力成本较高 的情况下,其净利率水平仅保持在 15%左右,远低于国内谐波减速器厂商。为了保 障一定的盈利能力,管理层不会进行激进的扩产政策。 根据我们测算,到 2027 年人形机器人达 100 万台量级时,全球谐波减速器产 能缺口达 1460 万台,其中约 200 万台来自工业机器人,1260 万来自人形机器人。 由于人形机器人的运动速度低于工业机器人,对谐波减速器性能的要求也低于工业 机器人,因此国内谐波减速器厂商可以胜任人形机器人对零部件的要求,在海外龙 头谨慎扩产的背景下,谐波减速器的产能缺口有望由中国厂商填补。
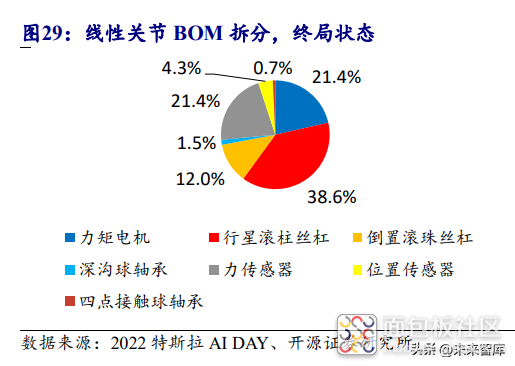
谐波减速器产品的技术迭代基本停滞,当前,我们认为应从扩产能力以及机电 一体化实力两个角度来衡量国内谐波减速器厂商的竞争优势。 第一,国内厂商和海外巨头之间的差异主要在保持产品一致性下的大规模扩产 能力。生产一台谐波减速器,从数理模型设计、材料热处理理解到设备选择、加工 工艺等环环相扣。具体过程是:首先设计柔轮齿型,柔轮的齿形决定加工设备的选 择,而设备的选择又决定钢轮使用哪种制造材料。目前国内外柔轮材料均使用 40CrMoNiA、40CrA 等碳合金钢。国内企业的材料热处理水平相差不大,但总体低 于国外水平。因此,钢轮加工技术路径的差异直接决定国内谐波减速器厂商产能释 放的快慢以及生产成本的高低。
第二,机电一体化能力。“机电一体化”,是指将精密减速器、电机及驱动器、 传感器进行组装形成一个基本传动单元,再通过控制器控制这个高度集成化的传动 关节以实现对本体的运动控制。机电一体化可以进一步缩小零部件体积,实现整体 运动控制,提高工业机器人等自动化设备的灵活性。 机电一体化是未来减速器厂商竞争制高点。全球谐波减速器龙头哈默纳科自 1977 年起生产销售机电一体化产品,陆续研发了伺服电机、驱动、传感器和控制器, 认为提高整体运动控制实力是实现技术进步的核心。哈默纳科作为引领谐波减速器 行业多年的龙头企业,其产业布局方案是判断行业趋势的风向标。同时,人形机器 人对关节小型、轻量的要求也在对机电一体化产品有更高的需求。因此,我们认为 机电一体化实力是谐波减速器厂商未来的竞争焦点。
1.3、关节轴承:用量超预期,可复用汽车供应链加速降本
特斯拉机器人关节处使用的轴承是支持旋转轴或其他运动体的机械基础件,可 以复用新能源汽车的轴承供应链,加速降本。 特斯拉机器人旋转关节使用 2 个角接触轴承,用来承受较高的转速的和一定的 轴向力。使用 1 个刚性强的交叉滚子轴承,同时承受较大的径向力和轴向力。线性 关节使用 1 个四点接触轴承,在高转速条件下承受双向较大的轴向力和径向力,以 及 1 个深沟球轴承。根据我们测算,当特斯拉机器人量产达到百万台量级,各类轴 承的单价均可降到百元以内,以 100 万台产量计算,带来的轴承市场空间增量约 37 亿元。 从供应链角度,深沟球轴承国内成熟供货,价格低,附加值低;角接触轴承国 内可供货,价格低,精度低;四点接触轴承国内可供货,价格低,精度低;交叉滚 子轴承国内少数厂家可供货,难度大。
我国轴承产业大而不强,高端轴承市场被以 SKF、NSK 为代表的国际厂商占 据,国内厂商以生产小型、中低端轴承为主。因此,国产轴承厂供应深沟球轴承、 角接触轴承以及四点接触轴承更具备优势。深沟球轴承设计简单,能高速运行并且 工作期间无需保养,价格低,是使用最普遍的轴承,国内已经实现成熟供货。交叉 滚子轴承是和谐波减速器配套使用,制造难度大,全球范围内可大规模量产的企业 少,主要包括日本 THK、日本 IKO、日本 NSK、日企哈默纳科和德国舍弗勒旗下 的 INA。国内谐波减速器龙头绿的谐波自研交叉滚子轴承,截至 2021 年年报已进 入中试阶段。
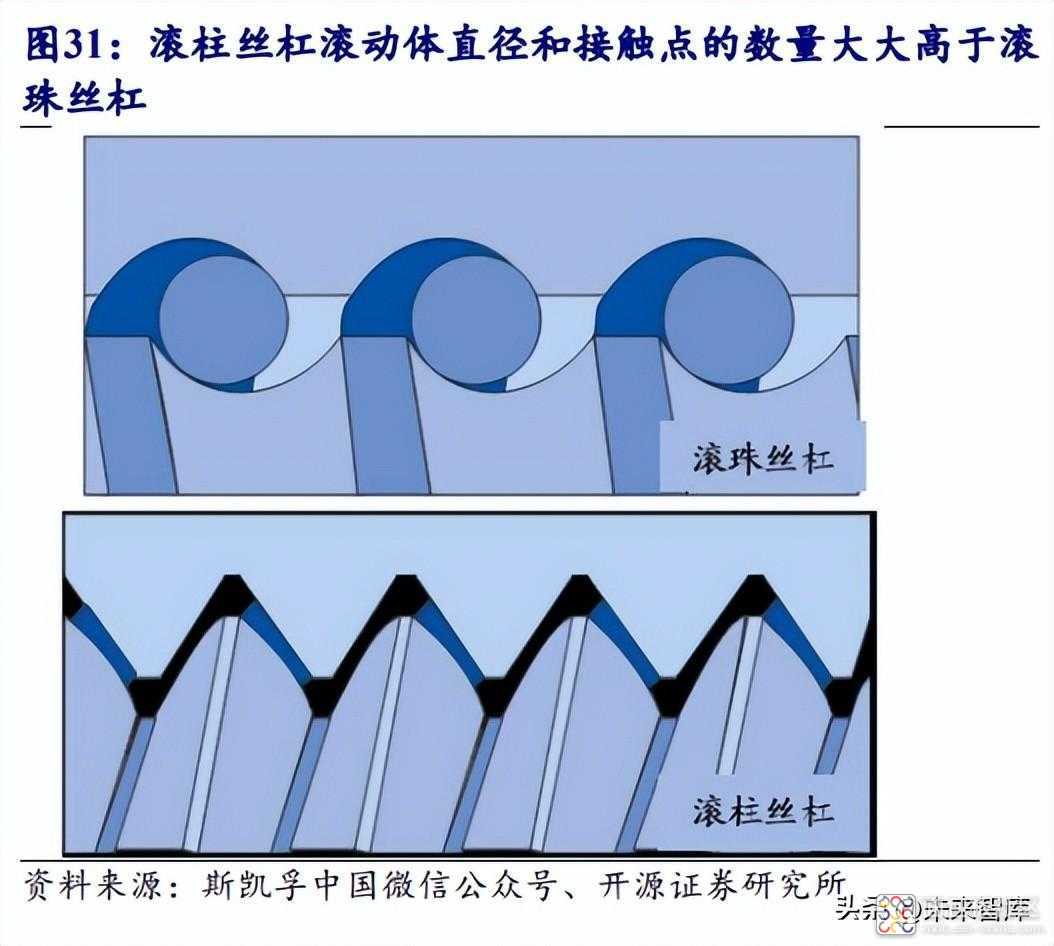
2、线性关节
特斯拉机器人全身使用 12 个线性执行器(亦成为伺服电缸),采用无框电机+ 滚柱丝杠的方案。丝杠的传动精度高,输出力能力强,但反驱透明度差(所以需要 力传感器),响应速度偏慢。这套驱动方案可以实现高刚性,但可能会限制下肢高 动态的运动能力。 线性关节是特斯拉机器人在硬件端优化升级的核心。特斯拉机器人线性关节采 用的通用伺服推重比从 1400N/Kg~4200N/Kg,其中自重较小的一款 0.36 公斤级别 的驱动器可能受限于尺寸及集成化的难度,导致推重比较低为 1400N/Kg,对比国 内先进的自重 0.1Kg 级别的微型伺服电缸推重比已达到 4900N/Kg,仍有较大提升 空间。
根据我们测算,行星滚柱丝杠、倒置滚柱丝杆是线性关节中价值量占比最高的 零部件,行星滚柱丝杠在特斯拉机器人硬件总成本中占比也最高。终局状态下,行 星滚柱丝杠、倒置滚柱丝杠相比早期阶段的降价空间分别达到 93%、95%。
2.1、滚柱丝杠
线性执行器和旋转执行器最大的不同在于使用了滚柱丝杠。 滚柱丝杠是滚珠丝杠的一种细分品类,制造难度比滚珠丝杠难度更大。滚珠丝杆是最常使用的机械传动元件之一。传统滚珠丝杆通过在丝杠和螺母之间引入滚珠, 能耗下降至低于 20%,因而摩擦降低,精度得以保持。而滚柱丝杠滚动体直径和接 触点的数量大大高于滚珠丝杠,因此承载力和寿命大大提升。 行星滚柱丝杠具有高承载、高寿命、高精度、高负载、高稳定性、导程小、响 应速度快、更清洁环保、更容易实现电控化等优势,将成为液压驱动、滚珠丝杠电 动缸的未来技术主力替代方案。在机器人、自动化行业,行星滚柱丝杠替代滚珠丝 杠电动缸和气缸;在机床、医疗器械、光学仪器行业,行星滚柱丝杠替代滚珠丝杠; 在汽车、新能源汽车、智能电车以及工程机械领域替代液压缸。
根据 Value Market Research 数据,2019 年全球滚珠丝杆市场规模为 195.48 亿美 元,预计 2026 年将达到 296.61 亿美元,期间年均复合增长率约为 6.14%。其中, 亚太地区是全球滚珠丝杆的主要市场,2019 年亚太地区市场份额占比为 43.56%,预计 2026 年将增长至 46.64%,亚太地区市场份额的快速增长主要源于中国等发展 中国家在航空、制造和机器人等行业的需求升级。 高精度滚珠丝杠技术壁垒高,海外厂商占据垄断地位。全球主要的滚珠丝杆厂 商有 NSK 日本精工、日本 THK、日本斯凯孚等。CR5 市占率达到约 46%。根据相 关数据,日本和欧洲滚珠丝杆企业占据了全球约 70%的市场份额。国内行星滚柱丝 杠生产商稀缺,仅有少量具备小批量研发制造能力的企业。
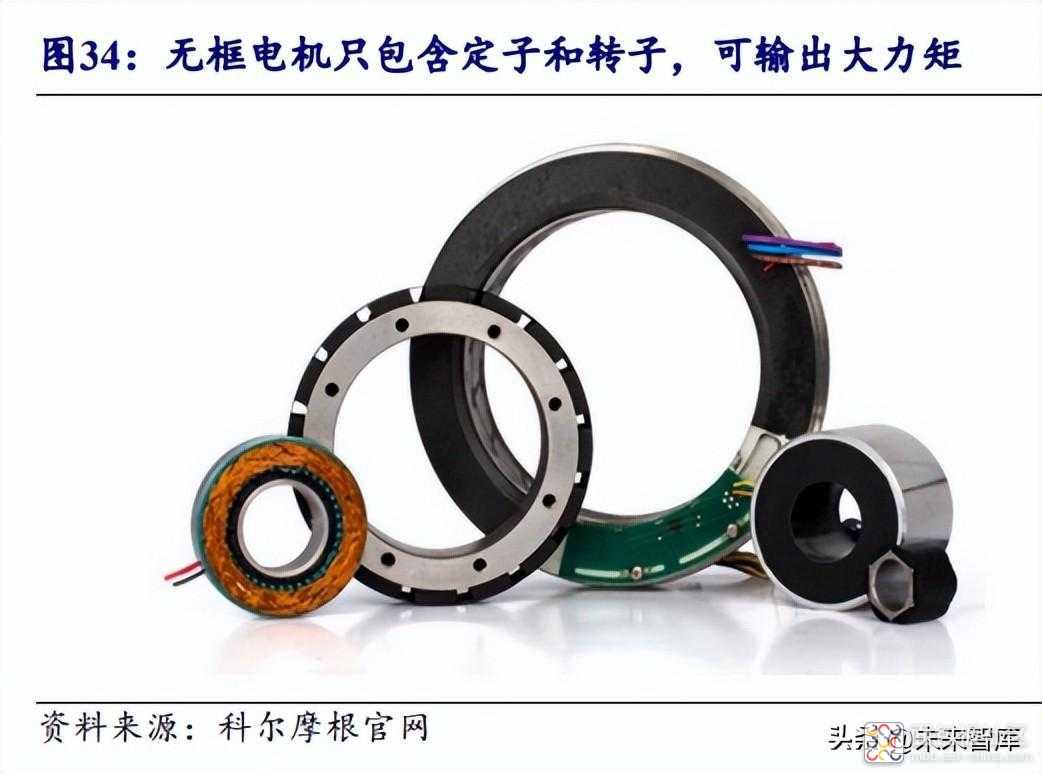
2.2、机器人关节高功率密度的选择:无框电机
特斯拉机器人线性、旋转关节处使用的无框电机是去掉轴、轴承、外壳、反馈 或端盖的伺服电机,只包含定子和转子。无框力矩电机的核心优势是输出力矩大、 结构紧凑,散热性好。1949 年由美国 Inland 电机公司(1960 年和科尔摩根光学公 司合并为科尔摩根公司)发明,用于早期导弹和空间飞行器的惯性制导系统上的传 动万向节。现在,无框电机的典型应用包括机器人和机器人关节、武器站、传感器 的万向节、瞄准系统、无人机推进与导航、工厂自动化设备等。 海外厂商科尔摩根、Maxon、日本电产、Moog 电机位列全球无框电机市场第 一梯队,国内供应商包括步科股份、昊志机电。
3、灵巧手:关注率先实现微型线性执行器量产的企业
特斯拉机器人的灵巧手的技术和现有人形机器人灵巧手一致,单手共 6 个自由 度 11 个关节,可抓起 20 磅重量,既可以完成大口径物体抓取,同时也能满足抓取 精巧物体的需求。从 2022 年特斯拉 AI DAY 上展出的视频可以看到,目前特斯拉机 器人灵巧手的设计优先满足大口径物体的抓取,适用于在总装线上进行物体的搬运。 也验证了特斯拉机器人将率先在汽车总装产线上投入使用。 以因时机器人为代表的厂商在机器人灵巧手方面已拥有全球领先的技术实力。 衡量灵巧手性能强弱的指标是单个手指可施加的力,目前全球领先的水平是单个手 指施加 1kg 左右的力,而因时机器人灵巧手单个手指可以施加的力已经能到达 3kg。
特斯拉机器人灵巧手内部构成是一个微型的线性执行器(伺服电缸)。内部通 过高速运转的空心杯电机(小功率段体积最小、功率密度最高的电机)提供动力, 搭载小模数齿轮的减速箱起到类似于旋转执行器的能力。高性能的螺杆结构使整体 结构更为紧凑。整个微型线性执行器由低压驱动板来控制。国产厂商在除了减速箱以外的其他零部件领域均处于量产的布局期。在特斯拉机器人的拉动下,能够率先 实现微型线性执行器量产的企业将通过规模效应大幅降本。
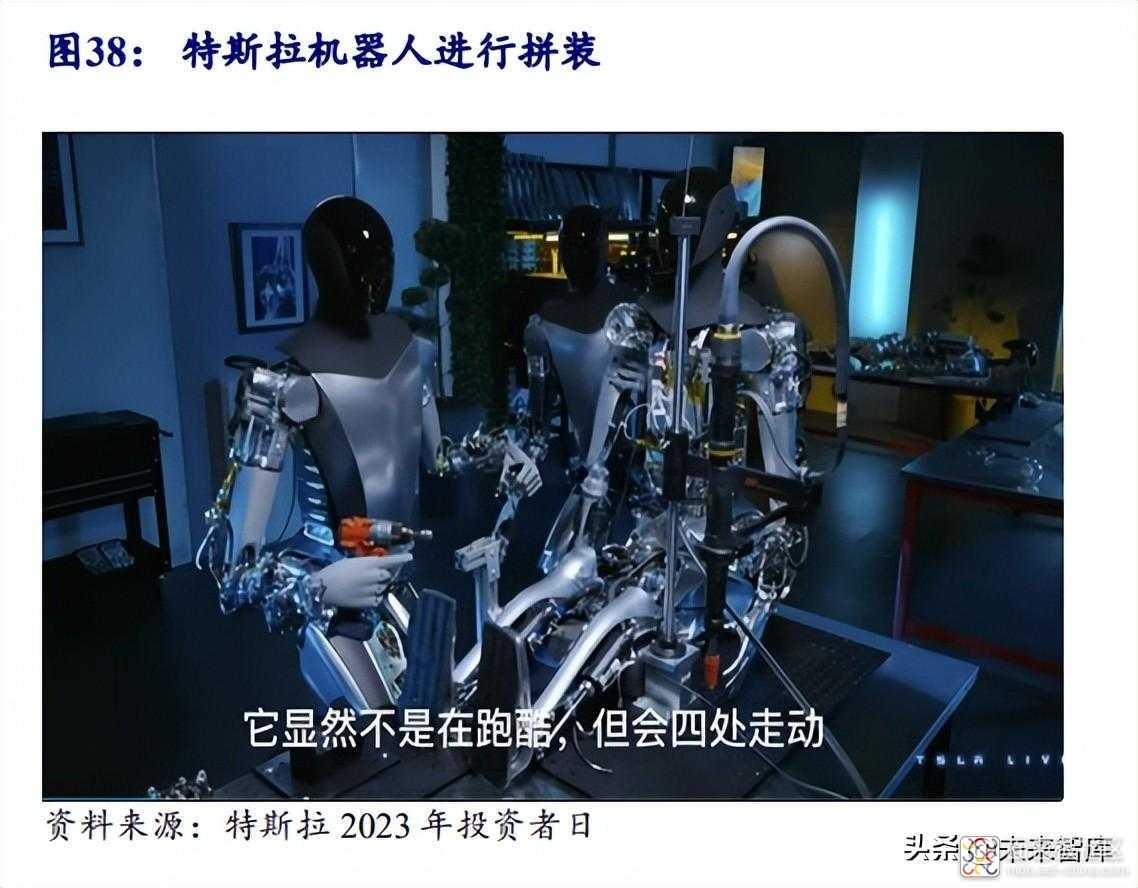
4、国产加工设备取得长足进展,为零部件厂加速扩产保驾护航
磨床和齿轮加工机床属于金属切割机床,是减速器、轴承、滚珠丝杠、电机在 精加工阶段的重要设备。齿轮加工机床主要包括磨齿机和车齿机,磨床包括螺纹磨 床和外圆磨床。磨齿是齿轮精加工的主要工艺,通过可靠有效地加工硬齿面齿轮, 修正热处理产生的变形和粗加工的各项误差,提高加工精度。目前,国产数控磨齿 机已取得了长足发展,各项性能比肩海外品牌,差距在于精度的保持程度,即,设 备是否可以满足每一个生产出的零部件都维持同样的高标准。 国产精加工设备取得长足进展,保障国内机器人核心部件厂商扩产。
国内秦川 机床、宁江机床(未上市)、北平机床(未上市)目前都已具备批量生产高精度齿 轮加工设备的能力。截至 2022 年 H1,秦川机床的磨齿机年产能 300 台,单台磨齿 机每月可加工 1 万件汽车齿轮,可用于其 RV 减速器生产线。中大力德、双环传动 也曾是秦川机床滚磨齿机的客户。宁江机床和华中数控紧密合作,设备已用于航空 航天等高精度领域。
5、其他零部件:电池、视觉传感性能优异
特斯拉人形机器人的电池容量 2.3kWh、动力电 52v,金属外壳保护提高安全性。 电池实现小体积大容量,推测复用了汽车动力电池技术。电池与主板、散热风扇置 于胸腔中。 视觉传感器硬件为左右单目相机+鱼眼相机,硬件成本较低,依赖算法。集成 了汽车视觉传感的技术,实现精确的 3D 建模。工厂等部分场景有应用 GPS 传感器。
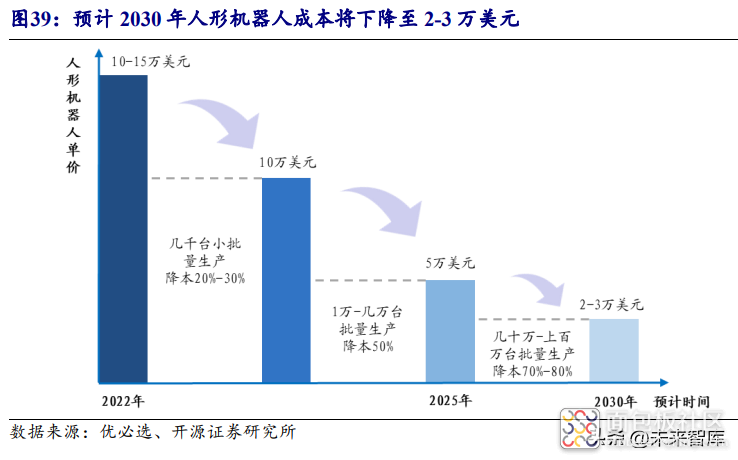
来源:未来智库